10 Critical Reasons Why You Need a Below-Slab Vapor Barrier
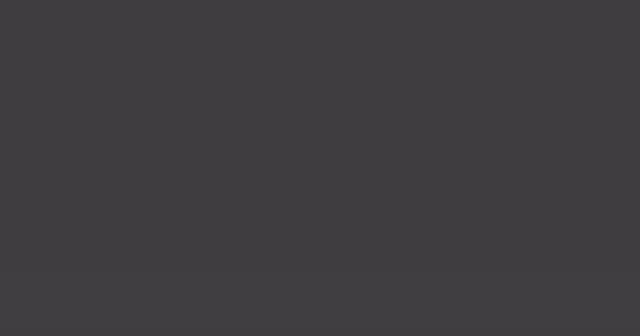
Despite its cost being measured in mere cents per square foot, project designers, contractors, and building owners often disregard a high-performance under-slab vapor barrier. Yet, failing to use this vital material may be the best illustration in the construction industry of “a penny wise and a pound foolish” – unnecessarily risking costly consequences and potentially years of legal squabbling over liability.
Here are 10 critical reasons why you should always use a high-performance vapor barrier, no matter the project:
1. Vapor barriers are relatively inexpensive. Floor failures are not.
The single most important reason you should use a high-performance vapor barrier is to protect the expensive floor covering in your building.
Water-based adhesives used to secure your floor covering are highly susceptible to degradation in the presence of liquid water and the alkaline salts it pulls into solution from the concrete slab. This creates a high-pH environment. Liquid water below the slab can diffuse through the slab as vapor, then condense under the flooring, which can re-emulsify some adhesives and damage others, thus destroying the floor covering. Water vapor diffusing through the concrete slab can also lead to deformation and discoloration of the floor covering material, leading to costly repairs or even replacement.
The cost of a vapor barrier – installed on the foundation before concrete placement – is far more economical than these nightmare scenarios.
2. A proper vapor barrier installation can limit your liability.
The concrete foundation of your building may feel rock-solid. Concrete, however, is, in fact, a porous material. Water vapor will always move from a higher partial water vapor pressure environment -- a function of temperature and relative humidity -- typically found below the building into regions of lower partial water vapor pressure, like conditioned interior spaces – even through concrete. That’s why nearly every expert in the concrete industry recommends a below-slab vapor barrier to stop the vapor drive of water upward and into your building envelope.
The group of industry experts at the American Concrete Institute committed this to their guide, ACI 302.2R in 2006. Moreover, most building codes have also codified the practice of installing at least minimal vapor protection below concrete slabs on grade and in most crawl spaces.
By opting to save relative pennies in material costs, some project designers, contractors, and building owners are electing to ignore industry best practices. In doing so, they’re exposing themselves to liability concerns that could come in the event of a floor failure or other problem with the building that arises from the migration of water vapor or other soil gases that could have been prevented by a vapor barrier.
3. Your indoor air quality may depend on it and so do the building inhabitants.
What’s that smell inside your relatively new building? It might just be the smell of ignoring the need for below-slab protection. Water is critical to mold growth in any environment; but while you might be quick to clean up after a spill to avoid mold growth, there is no cost-effective way to protect your building from the moisture that will enter your building from below if you failed to install a high-performance vapor barrier below your concrete foundation.
Moisture, however, may be the least of the problems passing through the concrete foundation that can negatively affect the air quality inside your building. Radon, for example, is the second leading cause of lung cancer in the United States, and the leading cause among non-smokers. A below-slab vapor barrier can also help prevent sub-slab radon ingress. Many vapor barriers are synonymous with soil-gas retarders in construction language. When evaluating the performance qualities of vapor barriers as soil-gas retarders, be sure to check the radon diffusion coefficient of the material before you select it. While there are many factors to consider, a general rule of thumb is: the lower the radon diffusion coefficient, the better and proper installation becomes critical in these scenarios, so make sure to follow the installation instructions and use the recommended sealing accessories.
Finally, the same adhesives that can be affected by liquid water and high-pH environments (destroying your floor covering) can also create issues with indoor air quality. A floor covering failure due to ignoring below-slab protection may be the insult, but the health impacts of the poor air quality from broken-down adhesives could lead to real injury of your inhabitants.
4. Even a warehouse can experience moisture problems.
Save the materials and equipment that are placed on top of exposed concrete. The peril of ignoring below-slab vapor protection in your building does not begin and end with the floor covering and its inhabitants. One of the classic mistakes builders make in storage facilities and warehouses is the impact moisture vapor can have on expensive inventory that must be replaced if damaged.
The penny-wise and pound-foolish rationale for a warehouse goes like this: it’s just an exposed slab. There’s no floor covering. There are few inhabitants and plenty of air circulation. What does some extra moisture vapor really matter? Why not save money and skip using a vapor barrier?
Here’s the problem with that logic: the moment you start putting materials down on the exposed concrete, those items become vapor barriers. Moisture will have a harder time moving through product inventory and its packaging and will instead begin condensing and pooling on the floor below, in the right (or wrong) conditions. That accumulation of water can destroy sensitive products. Chances are – replacing them will be much more expensive than installing that high-performance vapor barrier in the first place.
Don't forget about potential warehouse transformations in the future. Take the same foolhardy logic of the builder who removes below-slab vapor protection from the design of their warehouse or storage facility project and take it another step: what happens when the building needs to be reconfigured for another use?
Without a high-performance vapor barrier, installing a floor covering may be impossible (or violate its warranty – more on that later).
Protecting your foundation before concrete placement increases the adaptability of a facility for future use. This can increase the flexibility and desirability of a site for a potential buyer with designs on converting the facility for a different purpose.
5. Give your HVAC system a break - and maybe save some money in the process.
HVAC systems in cooling mode naturally remove moisture from the air. By forgoing the installation of a below-slab vapor barrier, you ensure a greater amount of moisture entering the building from underneath your building’s foundation.
Even without humidity controlling systems, this can mean more work for your HVAC system. The more your HVAC system is working, the more money you are paying in electricity costs. That’s one small reason why most green building codes and best practices include a high-performance vapor barrier in their specifications. A more energy-efficient building is better for the environment and your bottom line.
6. Your floor covering warranty may require it.
In some instances, not only is a below-slab vapor barrier strongly recommended, it can be required. Choosing to ignore the fine print of your floor covering warranty could drastically impact the effectiveness of your installation. Save yourself the headache associated with repairs and unwanted costs by reading the fine print of your warranty before starting your building project.
7. "Concrete Cancer" prevention.
It’s every bit as bad as it sounds: Alkali Silica Reaction (ASR) is commonly referred to as “concrete cancer.” In ASR, the common salts found in cement (alkali) react with certain forms of reactive, amorphous silica found in some types of aggregates to form a gel. Once the mature slab’s internal relative humidity reaches 80% or greater, the gel expands; the result can be destructive enough to close joints and cause irreparable cracking to your slab.
The only easily controllable variable in the concrete cancer equation is the moisture. If you’re using Portland cement concrete, you will have alkaline salts in the slab. Depending on your geographic location, you may also not be able to eliminate the amount of reactive silica in your aggregates. But you can control the amount of water entering your slab by using a high-performance vapor barrier. Call it cancer prevention for your concrete.
8. Consider potential benefits of an under-slab vapor barrier in reducing efflorescence.
Sweating Slab Syndrome may not sound as dire as “Concrete Cancer,” but the results can be a big headache for building managers and a major liability concern for owners.
It happens like this: liquid water on a slab can naturally pull salts to the surface of a slab and deposit them there as the water evaporates in a process known as efflorescence. Those are the white, flowery blemishes you often see in concrete. Many of those salts are hygroscopic, which means they absorb moisture from the atmosphere. This moisture deposits on the surface of the slab and causes damp and slippery conditions.
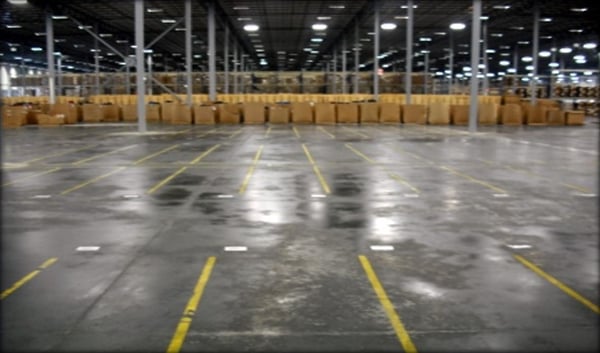
A mop or a “wet floor” placard may be a temporary solution – but the saltiness (the efflorescence) doesn’t evaporate with the water. The next time humid air hits the slab in your facility, the slab will “sweat” again, and the slip and fall hazard returns. Keep that mop or placard handy.
An under-slab vapor barrier won't eliminate all the factors that are most responsible for cases of sweating slab syndrome. In some cases, a culprit or contributor is efflorescence left when vapor-impermeable items are moved and the moisture beneath them evaporates, leaving efflorescence that can contribute to this issue
9. A high-performance vapor barrier prevents long-term curling.
This might be the biggest misconception when it comes to vapor barriers: their impermeability to moisture does not allow a newly-placed slab to dry evenly out of the bottom of the slab, as it does from the top. This disproportionate drying may lead to minor, short-term curling in the slab's early life, which will often subside as moisture gradients in the slab subside over time. However, the arguably more serious issue for a slab is long-term curling over the lifetime of the concrete foundation, which a high-performance vapor barrier helps prevent.
Without a vapor barrier, moisture would continually wet the bottom of the slab, as vapor will continuously drive from the high humidity below slab to the relatively low humidity above the slab. Without a vapor barrier in place, a slab that dries from its top surface will be exposed to disproportionate moisture levels in the slab for its entire lifetime. This can be a far greater curling threat to the foundation, long-term.
10. Vapor barriers can save time and money for the concrete placement team.
The penny-wise and pound-foolish may think forgoing the installation of a vapor barrier can save them time and money. But in the long run, the pennies-on-the-dollar that a high-performance vapor barrier costs can provide the concrete placement team plenty of opportunities for savings of both time and money.
First, a vapor barrier provides a consistent, smooth surface for concrete placement teams. This can be a time-saver where the placement team has a predictable surface on the site throughout.
Furthermore, placing concrete directly on the vapor barrier’s consistent surface can make finishing of the slab more even. This will provide the placement team better results and happier customers.
Be Vapor-Wise, Not a Pound (of Problems) Foolish
You only have one chance to make the right decision for your below-slab vapor protection: before the concrete is placed. Choosing to install a high-performance vapor barrier in your design will save you from headaches and more expense in the future.
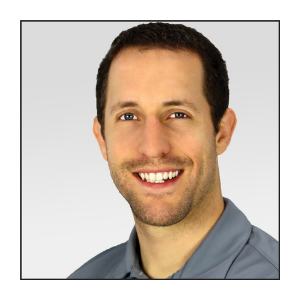
Written by Dan Marks
Dan Marks was the former Technical Director at Stego Industries, LLC.
- Stego (26)
- StegoCrawl (24)
- Stego-Awareness (17)
- Case Studies (14)
- StegoHome (14)
- StegoCrawl-Consideration (12)
- StegoCrawl-Awareness (11)
- Customer Stories (9)
- Stego-Consideration (9)
- Pango (8)
- Beast (7)
- StegoHome-Awareness (7)
- StegoHome-Consideration (7)
- How to Install (6)
- Drago (5)
- Pango-Awareness (5)
- Beast-Awareness (4)
- Beast-Consideration (3)
- Drago-Awareness (3)
- Pango-Consideration (3)
- Stego IQ (3)
- Drago-Consideration (2)
- StegoCrawl-Decision (2)
Popular Posts
Stay Connected.
Enter your email below.
Post Comments