Still Wet-Screeding? 6 Money-Saving Opportunities For Slab Placement
A Solution to Increase Profit, Crew Efficiency and Results During Concrete Placement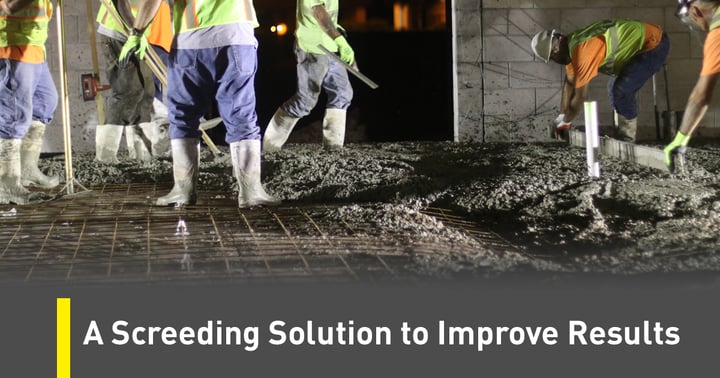
Wet-screeding, unfortunately, is an all too common practice in the concrete industry and is prone to a number of money-wasting inefficiencies when it comes to concrete placement.
The practice of wet-screeding began to take hold in the industry when high-performance vapor barriers and retarders arrived on our job sites more than two decades ago. Floor failures, mold growth and other slab tragedies told designers and builders they needed better below-slab protection from water vapor and other soil gases.
These new membranes immediately set in place one critical, new practice: never puncture the vapor barrier! Instantly, all kinds of screed hardware and their respective concrete placement techniques—developed over decades -- became obsolete.
Enter: wet-screeding. A crew member sets grade, usually with a laser level, then floats a “cow patty,” or wet pad, a small circle in the freshly-poured concrete, to denote grade for the crew striking off the concrete. No more screed hardware or stakes driven into the subgrade – a sort-of floating system.
I call wet-screeding’s influence over the concrete construction industry “unfortunate” because an experienced concrete foreman will tell you, profitable concrete construction comes from first-rate preparation and a constant focus on crew efficiency, which in turn comes from continuously educating and evolving with new technology and improved methods. Wet-screeding, for all its use in the construction industry, does none of these things.
Throughout my four decades in the concrete construction industry, I’ve worn many hats: I started on the end of a shovel in a ditch while still in high school, worked my way up to become vice president and general superintendent of a large contracting firm, and ran the concrete division of a major supplier in the industry.
After all these years and hundreds of thousands of yards of concrete, it’s easy to spot inefficiency and opportunities to save money when I watch crews place concrete.
That's the challenge, right? Concrete contractors need to consider these six factors they may not know could be eating into their bottom line. But do not worry, there is a solution and I will share it with you in this article.
#1: Cow Patties Can’t Withstand the Organized Chaos of the Job Site
Pouring concrete is organized chaos. Workers are tromping around in concrete boots, stumbling over rebar and other slab components. You don’t even need to step directly in a cow patty to affect its elevation.
I have a favorite video I took on a job site: a crew member floats a cow patty, after establishing the grade, he moves out of the way of the crew with the screed board. Another person – not on the screed crew -- walks by and steps on a piece of rebar that happens to be in a spread footing. When he steps on the rebar, which isn’t supported well, it goes down under his weight. When it does, it takes the cow patty right down with it – grade lost!
Of course, the crew member on the screed board didn’t see this and uses that compromised cow patty as his elevation marker.
How many cow patties did you float on your last wet-screed job?
Can you account for all your crew member’s movements, all the time?
What about any other trades working in the same proximity?
The scenario I depicted here has hundreds – if not thousands – of opportunities to happen on every concrete placement. The higher the slump, the more problematic this becomes.
#2: The False Sense of Security from a Laser Level – Human Error
Laser Levels: super hi-tech, right? Laser levels may be providing you a false sense of security along with all the other human error that can go into wet-screeding.
- Accidental Human Interference
Let’s assume your laser is calibrated and working properly, though we all know that someone bumping into your laser and throwing off your grade can happen in the organized chaos outlined above.
The crew member responsible for establishing elevation is going to be constantly leaning over to float cow patties in the fresh concrete. Anyone’s natural inclination in that position – leaning over with a grade rod in our hand – is for that rod to lean with you. The laser is counting on you to stand up straight while checking grade. We know humans, on the other end of that laser level, are not as consistent. - Concrete Buildup on the Grade Rod
The grade rod itself can also cut into your accuracy. As the concrete placement wears on, that grade rod – whether it’s a sophisticated, sectioned-off grade rod or just a scrap piece of wood –could build up concrete on the end that’s repeatedly dipped into the fresh concrete to establish level. That concrete buildup can potentially create another false reading and continue along from cow patty to cow patty. - Steady Hands Can’t Fight Off Natural Impulses
Finally, the biggest human error of the laser grade exists in the neural pathway between that crew member’s [hopefully] steady hand and their brain. Even the steadiest hands and the quickest nerves on a job site cannot set grade off a wet cow patty the same way they can off a fixed object and establish a grade consistent enough to achieve some of the floor levelness (FL) numbers being demanded on high-performance floors.
If you’re one of the few able to achieve these high standards while still wet-screeding, your consistency is benefitting your operation. Wouldn’t you want to know about a more consistent way?
#3: Crew Efficiency is Everything
Having served as vice president and general superintendent of a construction company, I understand the time constraints, competitive pressure and cost controls that can crush profit.
As tough as this dynamic is to work within, a lot of those pressures were outside of my control. Of course, I wanted to mind the price of ready-mix concrete and other big-ticket items, and make sure that we weren’t purchasing unnecessary supplies and accessories.
But there was one thing entirely within my control: my labor cost. If I paid close attention and managed my labor, I stood a lot better chance to make money. If I didn’t, I was subject to lose money. Pretty simple.
When you translate that to wet-screeding, I want my crew to move efficiently and work as a cohesive unit. I want them to be aware of the pitfalls I’ve outlined above, from unsettling cow patties to keeping their grade rods clean and plumb for accurate readings. When the mud hits the ground, you can tell the crews that understand this from those who don’t.
#4: Once the Concrete Hardens, Poor Results are Very Difficult to Correct
Concrete hardens. This is not an earth-shattering revelation. However, unlike many other aspects within the construction environment, problems with your slab are very, very hard to undo. They typically involve some sort of demolition equipment, which will generally involve a process that wipes out any profit you may have enjoyed on the job.
This dynamic in concrete construction is not exclusive to wet-screeding. My point is meant to put a punctuation mark on the ways wet-screeding may have brought you to a negative result once the concrete has cured.
Did you meet the FL numbers specified for the slab?
Is there pooling or ponding in low spots?
Humps in the floor or other problems?
If so, you’ve probably just lost money on your slab placement.
#5: Learn Lessons On and Off the Job Site
Crews very much need to prepare and communicate on the job site prior to a hard day’s work. Is everyone working as a team? Does everyone feel they have the license to speak up to improve something they see during the concrete placement?
But it’s the lessons learned off the job site that I believe many concrete contractors are ignoring. Habits in the construction industry are extremely slow to change, but it’s time to stop saying we’re under too much time pressure or cost constraints to get crews trained up on the latest best practices and changing technology in our industry.
This is a crutch; being stuck in this fixed mindset is leaving many concrete crews behind the profitability curve. The most successful firms I work with tell me they’re constantly staying up on the latest technology and training for their crews. If you find yourself nodding your head, you’re probably one of them.
#6: Prepare for the Next One
Finally, the biggest reason I believe wet-screeding currently has a hold on the concrete construction industry is this: it requires very little preparation. The process is, by and large, a seat-of-the-pants operation once the concrete starts flowing.
Most crews understand the site must be prepared, the subbase compacted, the vapor barrier installed properly, and hardware and formwork installed correctly prior to concrete placement.
Profitable crews, however, look for other approaches that give them an advantage to prepare before the concrete arrives that will make them more efficient when the organized chaos begins. In other words, don’t fly by the seat of your pants.
Identifying Problems was Easy, So I Invented a Money-Saving Solution
After four decades of watching these different factors cut into the profits of my company, my distributor relationships, and my customers, I got to work on a solution to improve the process of wet-screeding.
The solution = Beast® Screed and I trust it to help you turn a profit on your next project. Here is what it can do for all the previously mentioned money-wasting, inefficient results from traditional wet-screeding.
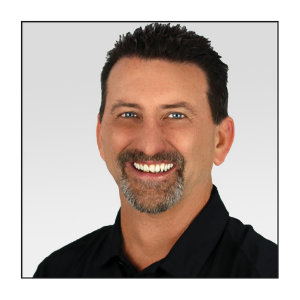
Written by Steve Lutes
Steve Lutes was the National Product Manager for Beast® concrete accessories at Stego Industries, LLC.
- Stego (26)
- StegoCrawl (24)
- Stego-Awareness (17)
- Case Studies (14)
- StegoHome (14)
- StegoCrawl-Consideration (12)
- StegoCrawl-Awareness (11)
- Customer Stories (9)
- Stego-Consideration (9)
- Pango (8)
- Beast (7)
- StegoHome-Awareness (7)
- StegoHome-Consideration (7)
- How to Install (6)
- Drago (5)
- Pango-Awareness (5)
- Beast-Awareness (4)
- Beast-Consideration (3)
- Drago-Awareness (3)
- Pango-Consideration (3)
- Stego IQ (3)
- Drago-Consideration (2)
- StegoCrawl-Decision (2)
Popular Posts
Stay Connected.
Enter your email below.
Post Comments