Concrete Moisture Testing – 5 Tips to Avoid Flooring Failures
Need to Achieve Slab Moisture Conditions Required by Your Floor Covering Manufacturer's Warranty? Consider the Following Factors When Testing the Moisture Level of Your Concrete Slab.
Background
In the late 1990’s, the Environmental Protection Agency (EPA) restricted the content of organic solvents in flooring adhesives and across a range of other product categories. These former solvent-based products contained volatile organic compounds (VOCs) that could cause adverse health effects like eye, nose, and throat irritation, in addition to headaches, nausea, and were even linked to the development of some cancers.
The EPA ruling was a major step forward in improving human health in indoor spaces. Just a decade earlier, in 1985, the EPA found that organic pollutants were two to five times higher inside homes than outside. Indoors, these contaminants didn’t dilute – they concentrated.
The Effect on Flooring Installations
Like most changes in regulations, the EPA ruling caused a scramble within the construction industry and, in this case, the resultant change in the flooring industry was to switch from these restricted solvent-based adhesives to water-based adhesives. Unfortunately, these early versions of water-based adhesives did not prove to be anywhere near as functional in the same environment as their solvent-based predecessors.
Why? In short, water-based adhesives in contact with a high pH solution are more likely to break down. More specifically, most water-based adhesives begin to break down at pH levels of 10 and higher, whereas historically, solvent-based adhesives were more resistant to a high pH environment.
After the change to water-based adhesive formulations, the construction industry, and more specifically the flooring industry, began to experience flooring problems at a far greater rate than ever before.
As flooring problems increased, the adhesive industry feverously continued their efforts to improve the moisture and pH tolerance of their materials. Flooring problems increased to the point that a number of national building owners stopped using resilient flooring materials altogether, opting to replace bonded resilient flooring with polished concrete.
By definition, pH is a measure of hydrogen ions in solution. Without enough moisture to create a solution, pH is not a factor in the distress of flooring installations. However, solution chemistry can develop within the capillary and pore structure of a concrete floor slab when the internal relative humidity level is 85% and higher. All concrete slabs contain alkali salts that, when brought into solution by liquid water, can create an elevated pH level at the interface of the adhesive and the surface region of the slab. Reduce the level of moisture within a concrete floor slab to the point that solution chemistry does not develop, and pH does not become an issue.
Given what we know about pH, one can see that any development or re-introduction of liquid water to the interface of the adhesive and the surface of a concrete slab can have serious consequences: when there is sufficient moisture within a concrete slab to create a solution, alkali salts, which are naturally present at a greater concentration within the surface region of a slab, enter into solution and thus create a potentially damaging elevated pH condition. Most water-based adhesives begin to experience distress at a pH level of 10 or higher, if the adhesive remains in contact with a sustained high-alkalinity condition, the flooring assembly may fail.
While the change in adhesive formulation is not the only reason for the increase in flooring issues over the past several decades, it most definitely has played a major role which has led to:
- Hundreds of millions of dollars in flooring replacements,
- lawsuits, and
- lost revenue.
This is where moisture testing comes in.
Why the Moisture Level of a Concrete Floor Slab Should be Tested
There are several reasons why one needs to test the moisture level of a concrete floor slab that is scheduled to receive a floor covering or coating. First of all, most manufacturers of flooring materials and coatings require moisture testing and that the tested moisture level be at or below a certain level for them to warranty their products. Secondly, as previously discussed, without sufficient moisture within a concrete floor slab to create a solution, pH does not come into play.
Here are 5 Important Tips to keep in mind when moisture testing concrete floor slabs:
Tip #1: All slabs to receive resilient flooring are required by ASTM F710 to have an effective vapor retarder installed in direct contact with the underside of the slab. This is not optional. In addition, if a low-permeance vapor retarder is not in-place directly below the slab, the results of any type of moisture test cannot be relied upon as the moisture level within the concrete will increase once the slab surface is covered by a non-breathable flooring material or coating.
It must be understood that the relative humidity below every building slab in America will approach and very likely reach 100% regardless of the depth of the water table, or the amount of precipitation (National Academy of Sciences – National Research Council Publication 596).
There is only one opportunity to take the moisture from the ground out of play and it is before the slab is placed. In addition to the vapor retarder requirements in ASTM F710, ACI 302.1R-15 and ACI 302.2R-06 both state the need for a below-slab vapor retarder when moisture-sensitive materials are to be installed over, or placed on the slab, and that the vapor retarder be installed directly below the slab.
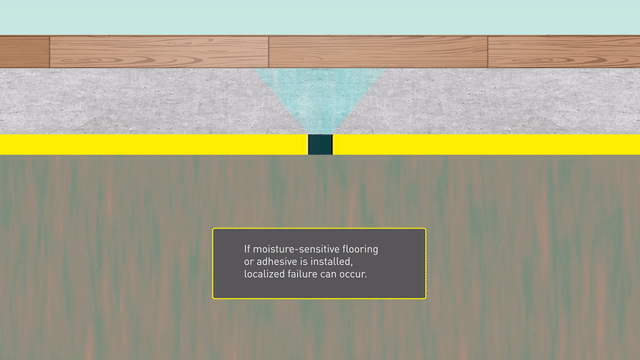
Watch this video to see how the water table below your building becomes a source of moisture directly under your slab.
Tip #2: Know the flooring manufacturer’s warranty conditions, including the concrete slab relative humidity requirements prior to flooring placement. Obtaining a warranty from the flooring and adhesive manufacturer is important, so it is advisable to know what you’re trying to achieve before you get started.
If needed, you can mitigate an unacceptably high moisture level in the slab right up until the time you are to apply the flooring adhesive.
Without moisture from the ground/soil impacting the moisture content of the concrete slab, another major benefit to taking ground moisture out of play with a vapor barrier is the improvement of the time it takes the concrete slab to achieve the flooring manufacturer’s moisture level warranty thresholds. An unsealed concrete slab will dry faster when placed directly on a vapor retarder than on the open ground (Brewer 1965).
Tip #3: Determine who will be responsible for conducting the pre-installation testing of the concrete floor slabs. In most cases, it is best for the owner to retain the services of an independent third-party individual or firm who is certified to perform the tests being required.
Note: In most cases, testing firms will conduct the tests and report the results, but they will not interpret the results. It is important to establish ahead of time who will be responsible for analyzing the data and deciding if it is safe to install the flooring materials based on the reported test results.
Tip #4: Determine which moisture tests will be conducted. There are several ASTM standard moisture testing methods that can be conducted. Sometimes there may be conflicting criteria/opinions between the construction documents, the flooring manufacturer’s installation requirements, and assumed best practices. If multiple moisture tests were indicated as necessary in separate documents, determine if one supersedes another, or if all will be required.
Tip #5: Some manufacturers or project specifications give you the option of performing ASTM F1869 (calcium chloride test) or ASTM F2170 (relative humidity probe). ASTM F1869 should not be used alone to base a flooring installation upon as the test does not provide sufficient information to base an informed installation decision upon. The test can provide a valuable piece of information, but the F1869 test procedure should never take the place of testing the internal relative humidity of the concrete. Use test equipment from a reputable manufacturer and make sure all necessary calibrations are conducted so that the results can be trusted.
Moisture testing professionals who are ICRI certified follow these instructions on a regular basis.
Don't Forget a Quality Below-Slab Vapor Barrier
A key takeaway here is that even if you identify the proper test locations, and have the moisture tests performed properly, if the ground is still in play, you may be headed for failure!
Without protecting the underside of your slab with a high-quality, low-permeance vapor retarder/barrier the flooring or coating installation will be at serious risk of future problems. Be sure to choose the right vapor retarder. Today many flooring and coating materials have permeance levels well below what ASTM E1745 considers to be adequate (0.1 perms [grains/(ft2*hr*in-Hg)]). A basic rule of thumb is that if what is on top of the slab is denser and less permeable than the vapor retarder/barrier below the slab, the moisture/humidity level within the concrete will gradually increase over time. It is highly recommended that owners and design professionals consider using vapor protection products with a permeance level less than 0.01 perms as measured before and after the conditioning tests required in ASTM E1745. This level of performance will go a long way in taking the ground out of play and providing adequate protection against floor covering and floor coating failures.
The change in adhesive formulations from solvent-based to water-based took place many years ago yet there remains today a significant number of flooring installations that experience problems. It is our hope that by increasing the level of knowledge concerning moisture, moisture migration, moisture testing, and moisture protection you can greatly reduce or eliminate the potential for a flooring or coating problem to occur on your projects.
If you have questions about how best to protect your upcoming project from the potentially damaging effects of moisture and alkalinity, please feel free to reach out to your local Stego representative who can answer all your questions.
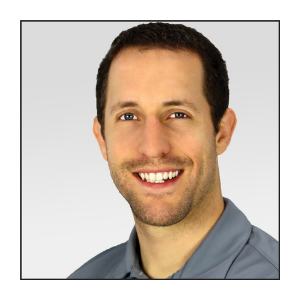
Written by Dan Marks
Dan Marks was the former Technical Director at Stego Industries, LLC.
- Stego (26)
- StegoCrawl (24)
- Stego-Awareness (17)
- Case Studies (14)
- StegoHome (14)
- StegoCrawl-Consideration (12)
- StegoCrawl-Awareness (11)
- Customer Stories (9)
- Stego-Consideration (9)
- Pango (8)
- Beast (7)
- StegoHome-Awareness (7)
- StegoHome-Consideration (7)
- How to Install (6)
- Drago (5)
- Pango-Awareness (5)
- Beast-Awareness (4)
- Beast-Consideration (3)
- Drago-Awareness (3)
- Pango-Consideration (3)
- Stego IQ (3)
- Drago-Consideration (2)
- StegoCrawl-Decision (2)
Popular Posts
Stay Connected.
Enter your email below.
Post Comments