Holes in the Under-Slab Vapor Barrier – Do They Matter?
Even Small Holes Can Lead to Big Problems
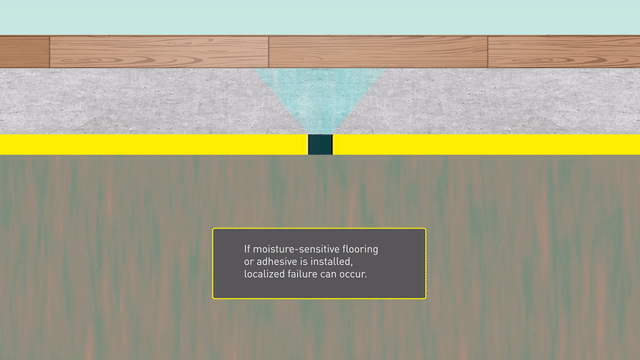
A working construction site can be brutal on the building envelope: coarse aggregate, tools, form stakes, welding sparks, and finishing equipment can all create holes in the below-slab vapor retarder. In some cases, contractors feel obligated to poke holes in the vapor barrier to help dry the slab.
This is the kind of “help” that keeps me up at night.
With how rugged the environment is – and how difficult it can be to spot holes in the plastic membrane – does it really matter if there are holes in my under-slab vapor barrier? What impact will holes have on moisture protection for my concrete slab?
Before we delve into the building science, ask yourself these practical questions:
- What is your tolerance for construction defects and liability on your project?
- Are you comfortable with your insurance coverage and potential premium hikes?
- Have you experienced a floor covering failure, including ripping up a concrete slab to determine whether there are unrepaired holes in the vapor barrier?
- How will the building owner respond to the business disruption of a flooring failure or the poor indoor air quality of a defective vapor barrier installation?
- Who’s the first to get the call in the event of a failure?
- Has the project team consulted with the vapor barrier manufacturer to troubleshoot installation challenges?
While rhetorical, these questions put a fine functional point on the more complex scientific conversation: an ounce of prevention in the construction industry is always worth far more than a pound of cure.
If you’re wondering if repairing holes in your below-slab vapor barrier installation is important, that’s the ‘why’. The ‘how’ -- how holes in the membrane can compromise indoor air quality or lead to a floor covering failure – is the building science.
ASTM E1643, the standard practice outlining the installation of under-slab vapor barriers and retarders, is clear in its core objective: to create a monolithic membrane between the slab we are seeking to protect and moisture sources from which water vapor can diffuse upward into the building envelope.
An additional factor beyond the building science and operational impacts includes the liability of having punctures in an installed vapor barrier. Concrete Contractors, General Contractors, and Design Professional would do well to avoid getting into a construction defect claim in the first place, but if a claim occurs, the integrity of the vapor barrier and proper installation can help reduce liability (and gives all parties the ability to illustrate compliance with industry recommendations/standards).
Aside from selecting a qualified product, a quality installation is also critical and very obtainable (in most cases) to execute with proper instructions. Scrupulous installation crews having just finished their “perfect” installation, may wonder:
- Does that hole create a superhighway for water vapor diffusion, wreaking havoc in the built environment?
- Should I be worried about holes in my under-slab vapor barrier? Do they matter, and how critical are repairs?
- Just as we might say that a coffee mug with a hole in it is no longer truly a “cup,” does an under-slab vapor barrier lose its function if it is not perfectly monolithic?
The answers to those questions can be found in how water vapor moves and the specific nature by which the first side of our building—the one under-slab vapor barriers and retarders protect— interfaces with the “outside” world.
Basic Background Science: How Water Vapor Moves into Buildings
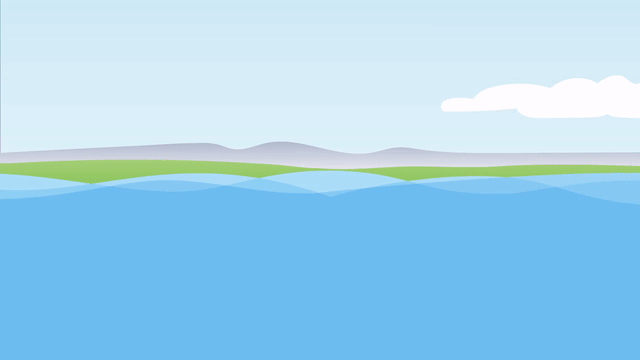
Water vapor—water’s gaseous form/phase—moves into buildings and building materials via two primary mechanisms.
1. Advection: occurs when water is carried into a building via/as part of an infiltrating bulk medium. Think about a flowing river—the medium of water moving carries with it all the sediments, dissolved gases, and other floating debris with it.
The medium with which we are concerned is air, that ubiquitous blend of oxygen, nitrogen, carbon dioxide (infamously), and, among a few other gases, water vapor. If a bulk pressure differential exists across any continuous volume of air, the air—all the individual gas molecules, suspended particulates, etc.—will move from regions of higher air pressure to those of lower pressure.
Rather than using the term “advection,” we often more simply just think about “bulk flow” or “air leakage”— and the water vapor the air “holds” and “carries” with it as it moves.
Two primary factors are at play when we consider advection and the built environment:
- The continuity of the building envelope. If a building envelope has holes or discontinuities, the air in the building and the air outside can exchange places by way of those holes.
- A difference in air pressure on either side of the envelope. Bulk flow occurs when higher pressure air moves to regions of lower air pressure. If a building is negatively pressurized—where the pressure inside is less than that outside in the atmosphere— then air will flow into the building, and the water vapor in the air will move with it.
2. Diffusion: Water vapor molecules zoom around randomly; but collectively, they tend to move from areas of higher concentration to those of lower concentration. This is true despite an individual molecule having no “knowledge” of what the concentrations of its fellow molecules are around it.
Via random motion, water vapor diffusion emerges by a statistical imperative, as regions with higher water vapor concentration have a higher likelihood of “sending” water vapor molecules to the regions with lower concentration. In our river analogy, if we dropped a bit of food coloring into the water, we would see that colored droplet spread outward, fading as it dispersed through the water. The food coloring would both be moving via diffusion and likewise moving via advection—both can and do happen cumulatively.
Diffusion occurs within a single continuous medium (think odor molecules from a scented candle diffusing throughout a room, or the food coloring example above), but it also happens in the movement of gases into and across other media (think of helium balloons slowly losing their lift and volume—helium diffuses across the balloon into the helium-poor air).
Water vapor molecules in the air are constantly moving into and out of almost all materials (our skin, tree bark, vapor barriers, etc.) they encounter. The process of moving from one medium to another is often called partitioning, and movement completely across, say, a plastic membrane—from the air on one side to air on the other— is referred to as permeation.
When more water vapor molecules…
1) partition from the under-slab environment into a vapor barrier
2) diffuse across the vapor barrier material
3) partition into the interior concrete/air (or other adjacent materials) then take the reverse path
…we see net “diffusion” – permeation -- the product of partitioning and diffusion of water vapor into our buildings. Imagine congestion on a highway due to overpass construction; if onramps are allowed easier access to getting on but exits are jammed up with road crews, making it harder to get off, traffic will get pretty bad.
Ok, I Understand the Science of Water Vapor. So, Do Holes in the Vapor Barrier Matter?
Let’s zoom in to visualize what a hole looks like in our system.
In Illustration 1, we see a high-performance under-slab vapor barrier sitting directly below a cast-in-place concrete slab. A small hole—maybe somebody dropped a piece of rebar—in the vapor barrier creates a discontinuity in this portion of the building envelope. The soil/subbase beneath underlying the slab system has a relative humidity of nearly 100 percent (regardless of the depth of the water table, this is inevitable).
Illustration 1 - Small hole in a below-slab vapor barrier sitting directly below a cast-in-place concrete slab.
Our first consideration: is advection possible through this hole? Assuming the building is negatively pressurized, can we see bulk airflow that will allow under-slab air into our building?
Notice that we have a continuous concrete slab directly over the hole in the vapor barrier. Concrete is porous, yes, but the pore structure is typically very fine. Air is not going to move through it easily (try breathing through a wet sponge—actually, don’t try this).
Over the slab we also very often apply monolithic flooring systems over the top of the slab, covering joints. Slabs are also typically cast over fairly dense subbases (e.g. certain native soil, or aggregate bases with sufficient fines).
In all of these examples, we have materials in place that choke off possible pathways that would otherwise allow air above and below the vapor barrier to communicate. Even if a pressure differential exists between the building interior and the environment below the slab, bulk airflow would be stymied.
For holes in our vapor barrier to be an advection concern, we need both:
1. A discontinuity in our slab/flooring/vapor barrier system. This may happen from bad luck, locating an unsealed control or construction joint in our floorless slab directly over the hole.
2. A subbase that is coupled with the atmosphere. This depends on how the subbase is designed, but certain to be the case when venting systems are used, common in radon mitigation systems and controls for other soil gases.
See Illustration 2 for an example.
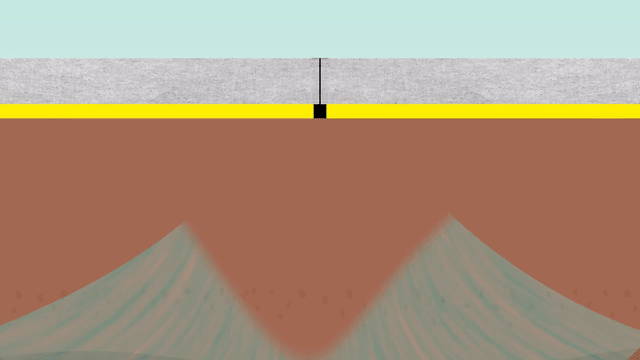
Illustration 2 - This clip demonstrates how vapor barrier holes can be an avenue for advection.
While it may seem unlikely that these stars may align, repairing holes in the vapor barrier makes sense. Repairs help to make our under-slab vapor barrier do double duty as something of an under-slab air (soil gas) barrier.
Our second consideration: is diffusion possible through this hole?
Yes, of course. The hole in the vapor barrier provides a localized area where diffusion is likely to increase. This is simply a matter of the relative resistance— between concrete/air and the vapor barrier materials— that the water vapor molecules below the slab encounter as they move upward.
A vapor barrier is made of materials that provide a tortuous path for water vapor movement, but those molecules will find their way through. The journey is long and arduous, like trying to cut your way through a lush jungle with a dull machete.
A hole in the vapor barrier is likely to be “occupied” by air or concrete. Intuitively, air provides very little resistance to vapor diffusion; concrete does provide some resistance to diffusion, but (at typical slab thicknesses) it is orders of magnitude less robust than the resistance provided by the vapor barrier (think of a sparse forest you could walk through easily, instead of that jungle you have to cut and claw your way through). Part of the reason this is true depends on the structure of concrete and the specific nature of cast-in-place concrete.
Concrete can be quite dense, but it is still porous! Furthermore, the pore structure of cast-in-place concrete tends to align vertically, based on the way concrete separates gravimetrically during initial placement.
Water vapor, in fact, encounters more resistance trying to move horizontally through a slab cast in place than it does vertically. As a result, the diffusion profile of under-slab water vapor diffusing through a concrete slab on or below ground slab might initially look, as shown in Illustration 3, conically shaped, spreading out upward from any hole in the vapor barrier.

Illustration 3 - Water vapor encounters more resistance moving horizontally through a slab cast in place.
If a moisture-sensitive flooring is installed, the areas outside of this cone are perhaps at less risk of being more immediately affected by this moisture. And it is possible that the amount of water vapor diffusing up from this hole is still small enough that it will never create the type of conditions that would cause a flooring issue or adhesive failure. Research by Bruce Suprenant and Ward Malisch, however, has shown that the local punctures in the underlying vapor barrier might have a significant effect on the moisture vapor emissions rate (MVER) from the concrete placed above. As ACI Committee 302 summarized in their ACI 302.2R-06 Guide for Concrete Slabs that Receive Moisture-Sensitive Flooring Materials:
“A 1/8 in. (3.2 mm) diameter nail hole allowed an average MVER of 1.3 lb/1000 ft2/24 h, and a 5/8 in. diameter stake hole increased the average MVER to 3 lb/1000 ft2/24 h. Because a 3-lb rate is often the maximum allowed for installation of moisture-sensitive floor coverings, stake holes of this size could conceivably cause localized floor covering failures or delay floor covering installation.”
Given these circumstances, you may have read that if a vapor barrier covers 95 percent of an installation, the user gets 95 percent protection. This is true but ask yourself: if five percent of your floor covering is destroyed as a result of the accumulation of unwanted water vapor diffusion, will it require you to replace 100 percent of the floor? Even one percent of subpar protection can be problematic over a long enough period of time and lead to an expensive (albeit more localized) problem. We should continue to always be vigilant to reduce holes in the vapor barrier to resist, across a slab footprint, diffusion of under-slab water vapor.
Other Ways Holes in Your Vapor Barrier Can Create Trouble
Holes in an air barrier or vapor barrier can lead to other issues as well. If liquid water finds its way to a hole in a vapor barrier, it can certainly cause problems. This is especially true if sand or other fill layer is used over the vapor barrier, between it and the slab.
Water—liquid, and vapor—that finds its way into a “blotter” layer (as it was often used to help excess mix water from bleeding through the surface of a slab after placement) can spread out across the footprint of the slab, potentially causing issues at areas far beyond the original hole.
Illustration 4 portrays another concern: the case of a high-water table.
Illustration 4 - Water that finds its way into a "blotter" layer can spread out across the footprint of the slab.
A slab cast directly on the vapor barrier can be affected by this source of liquid water as well—remember that vapor barriers are not necessarily waterproof, and waterproofing membranes may not be good vapor barriers. However, as was true in our examples pertaining to diffusion above, if a slab is cast directly above the vapor barrier, liquid water would be more likely to only affect a more localized area above and around the hole.
We should also keep in mind that there are other soil gases that could move into our buildings, through the slab or elsewhere, via diffusion or through air leakage. Radon is a prime example. We need not only concern ourselves with creating an air and vapor barrier below our slabs; we may also need to identify other potential discontinuities at the slab perimeter, so they can be sealed as well (which can often be done during the installation of the vapor barrier or post-slab placement with joint sealants).
Even Small Holes Can Lead to Big Problems
The differences between diffusion and advection betray an important fact: air leakage carries a lot more moisture into a building than does diffusion, likely by several orders of magnitude. This is one of the first points building envelope consultants will make, and it is a critical fact to know, primarily in above-grade applications. But for the under-slab and below-grade interfaces, since air exchange and bulk air movement is often limited, that difference fades; in fact, protection from diffusion becomes critical for combatting flooring failures and adhesive issues and reducing the potential for mold growth.
Holes in your under-slab vapor barrier or retarder are important to repair to minimize the potential adverse effects associated with both under-slab vapor diffusion and moisture infiltration due to bulk airflow. Best practices – ASTM E1643 specifically -- call for damaged areas to be repaired.
A single random pinhole is unlikely to spell doom for your project. Even several small holes across a project are not reason to lose sleep. But in my decades working in the science of water vapor diffusion and below-slab protection, I have yet to see a person walking around with a pin, poking holes. What I see all the time, however, are repeated punctures from temporary form stakes, far larger than a pin, adding up to a greater potential for trouble. I could write another entire article on that subject.
It’s best practice. Repairs are simple. And the consequences of a small problem could be expensive. Avoid holes in the first side of the building envelope.
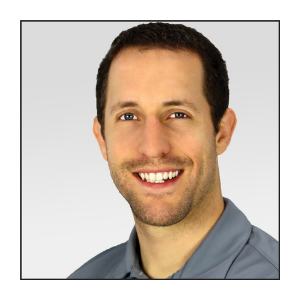
Written by Dan Marks
Dan Marks was the former Technical Director at Stego Industries, LLC.
- Stego (26)
- StegoCrawl (24)
- Stego-Awareness (17)
- Case Studies (14)
- StegoHome (14)
- StegoCrawl-Consideration (12)
- StegoCrawl-Awareness (11)
- Customer Stories (9)
- Stego-Consideration (9)
- Pango (8)
- Beast (7)
- StegoHome-Awareness (7)
- StegoHome-Consideration (7)
- How to Install (6)
- Drago (5)
- Pango-Awareness (5)
- Beast-Awareness (4)
- Beast-Consideration (3)
- Drago-Awareness (3)
- Pango-Consideration (3)
- Stego IQ (3)
- Drago-Consideration (2)
- StegoCrawl-Decision (2)
Popular Posts
Stay Connected.
Enter your email below.
Post Comments