Improving Concrete Formwork Without Sacrificing Your Vapor Barrier
Crucial Considerations for Project Teams When it Comes to the Vapor Barrier Installation
Concrete formwork goes at least as far back as the Roman Empire. If you know anything about cast-in-place concrete construction, you have to marvel at the Colosseum and the Pantheon for their beauty as well as for the remarkable ingenuity of the construction practices of their time.
It’s a useful reminder: many of the practices in concrete construction are, literally, ancient. Two millennia later, we still use wood to form concrete to a preferred shape and elevation that meets the needs of our buildings. After five decades in the concrete industry, some of my colleagues like to joke that I know these tidbits only because I was there to observe the construction of Ancient Rome.
While it may feel that way some days, my time in the concrete industry – from spending summers as a teenager on the end of a shovel, to inventing and patenting new products to make wet screeding more efficient and achieve better outcomes – has seen an age-old practice come into conflict with modern building science.
The Romans didn’t have the benefit of steel stakes to secure their wooden forms. And they certainly didn’t have highly engineered films – vapor barriers – to protect the underside of their buildings from water vapor and soil gases. These are the players in the 21st Century concrete slab design conflict.
Early in my career, we could hammer steel form stakes wherever we liked, to get wooden forms in place quickly and effectively. When high-performance vapor barriers came along, those of us who spent time considering best practices and how to deliver the highest quality instantly knew we had a problem: for interior forming, where a vapor barrier had been carefully installed and sealed, driving form stakes through the vapor barrier would simply undo all the reasons you installed the vapor barrier in the first place!
If you want to skip ahead, watch our step-by-step video to receive the materials, techniques, and tips to efficiently and efficiently create a vapor barrier-safe forming system.
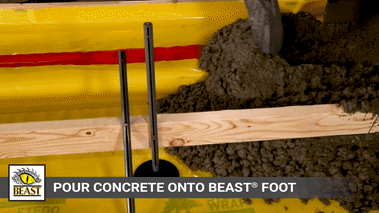
Consider the installation standard at play here, ASTM E1643. It states, no less than four times, the importance of how the material selected for installation should be able to resist puncture, and how the installation itself should not puncture the vapor barrier at all.
And yet, for the last two or three decades, since high-performance vapor barriers have gained adoption in the industry, some concrete crews continue to hammer away, driving steel stakes through the plastic membrane to set interior forms. I’ve been on job sites where I have seen meticulous, carefully sealed vapor barrier installations riddled with hundreds of three-quarter-inch holes from interior concrete forms being set.
Most knowledgeable people in the industry know we shouldn’t be doing this. I’ve even seen slab placement crews using things like sandbags to hold their interior forms in place, so they didn’t puncture the vapor barrier.
But that’s the thing about ancient practices: they’re ancient, right? Even when new solutions come along, if there isn’t a practical, repeatable process to deploy them, they don’t get implemented properly.
And so, as I write this, a member of a concrete crew somewhere is probably hammering a low-dollar stake into a vapor barrier installation that cost a thousand times more in material and manpower, ultimately jeopardizing the below-slab protection of a building many millions of times more valuable.
“It’s the way we’ve always done it.” If you don’t know there’s a better way (or haven’t been convinced yet), that’s what we’ve all said, and not just about forming concrete.
I get it. I was that guy on the jobsite once, too. Now a little older and wiser, I have good news: there is a better way to preserve well-placed formwork and protect the vapor barrier from punctures.
Before I get to the solution, my time in the industry has helped me understand that you can’t just offer a better solution and expect it to be instantly adopted. You must help those involved understand why those age-old practices are no longer safe, effective, and/or permitted.
Here are 5 perspectives of people I talk to frequently about these issues, and why each of them should care about all those needless holes in their vapor barrier installation.
Perspective #1: The Commercial Building Owner
This is usually the easiest conversation to have but is also with the one person that is literally and figuratively farthest away from all those holes happening in their under-slab vapor protection.
The commercial building owner is playing the long game. While construction schedules and budgets are incredibly important, they’re measuring their ROI by the square foot for the life of their building.
They’re also going to be the one present if a problem arises with their slab later on. In the case of those many holes in their vapor barrier, that problem is most likely going to be a floor covering failure – due to the diffusion of water vapor through the holes and the concrete.
As the property owner, I can’t imagine why they would knowingly subject themselves to this level of risk. Especially when those easy-to-make holes in the vapor barrier can lead to substantial downtime and cost to a building owner.
BUILDING OWNERS 📣 ask your slab designer, contractors, and inspectors what they’re doing to avoid this. You’re going to be the one losing ROI when a problem arises.
Perspective #2: The Slab Designer (Architects, Engineers, Consultants)
These are also very forward-looking conversations. Designers care about their specs, how their selections integrate into both form and function, and the standards behind these decisions.
In most scenarios, slab designers will likely consult ASTM E1643 to make important decisions about where to seal their vapor barrier installation and the performance characteristics they’ll need in product selection to meet the design and use of the building.What they might not consider when reviewing the standard, is how interior formwork might literally punch holes in their carefully designed plans. But they are likely to be the first people to receive a phone call from a building owner if a problem with this system comes up.
SLAB DESIGNERS 📣 hold your contractors and installers accountable to help protect your project and prevent liability. Ask them how they intend to establish the changes in elevation to the slab or other interior formwork without puncturing the vapor barrier.
Perspective #3: The General Contractor
This is where the rubber starts to hit the road or, for the sake of this analogy, where the concrete starts to hit the subgrade.
Alongside the many important decisions general contractors must make to keep projects running on time, they are constantly balancing the time, labor, and material considerations of their bottom line.
This most commonly comes up around material selection. It’s easy to see the bottom-line of the initial cost of goods. It’s not as easy to see the time and manpower expense sometimes associated with these so-called money-saving choices.
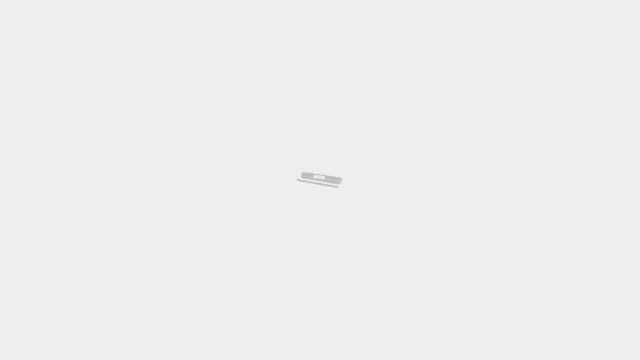
GENERAL CONTRACTORS 📣 if the ASTM standard says something, what is the likelihood an inspector might call attention to the vapor barrier installation riddled with three-quarter-inch holes? How much time, material, and labor will be required to fix this.
Perspective #4: The Residential Builder
The residential builder might be doing some of the work, and might be doing some of the design, but they are almost always the building’s first owner. They’re a lot closer to their subcontracted installation crews and they are usually the eventual owner of the home.
Residential building is lighter, smaller, and faster. But the best commercial construction practices, codes, and standards always migrate to residential work in time. In the case of under-slab vapor protection, that evolution is well underway: residential construction has moved away from 6-mil poly sheeting under their slabs to high-performance vapor barriers for better help with protection from water vapor and soil gases, like radon.
Homebuilders also have another consideration in this realm: the new home buyer is savvier and better-informed than ever. Information about the materials that go into their new home is just a click away. Many custom home clients are now calling for specific products to meet certain performance or sustainability ideals.
For both reasons, understanding the standard of installation for a high-performance vapor barrier is essential. You don’t want the first lesson in puncturing a vapor barrier to come from a code enforcement.
RESIDENTIAL BUILDERS 📣 it might be a good time to brush up on the most recent update to your local building code. Talk to your subcontractors about how they intend to protect the slab, and the means and methods they’re using to ensure that protection isn’t compromised.
Perspective #5: The Concrete Placement Crew
This is my favorite conversation to have because it’s the community I come from – I was a part of these crews for many decades.
I also understand the “this is the way we’ve always done it” sentiment. The economics of concrete placement is almost entirely about the cost of labor and its efficient deployment, and very little about the price of the commodity being installed. There is a very good business case to using tried and true methods, once you figure out how to do them profitably.
One of my favorite ways to approach these conversations is around the virtues of pride and quality. Almost to a person, concrete crews take pride in their work and want to do a good job. How can we do that if we’re punching hundreds of holes into our meticulously installed vapor barrier?
I would know. I did this job for years. For a long time, there was no good solution.
CONCRETE PLACEMENT CREWS 📣 I have good news for you. Stego has the solution.
Secure Form Stakes and Prevent Vapor Barrier Punctures with Beast Form Stake®
I remember the specific job site I was on when the light bulb went on in my head. I had already invented Beast Screed®, a more efficient way for crews to wet screed their slabs and avoid the imprecise results of using cow patties or wet pads. This screeding solution is held in place by Beast Foot®, an engineered peel-and-stick adhesive which sticks to the vapor barrier and can hold up to the rigors of a concrete pour.
Originally, a version of steel form stake, (screed pad post) was used with Beast Foot to support interior forms. But the versatility just wasn’t there: steel form stakes have pre-drilled holes. When you’re banging them into the ground, it’s easier to drive them to the required depth. When you can no longer do this, you can get stuck quickly.
That’s how I developed Beast Form Stake: its lightweight plastic material is very easy to work with but still durable. I’ve watched forms supported by Beast Form Stake and Beast Foot get racked by a concrete pump for hours without coming undone. And most importantly, Beast Form Stake features a SpeedTrack™ fastening groove, which allows forms to be nailed, or screwed, any place along the length of the stake. And, like steel form stakes, they can be cleaned and reused repeatedly.
Concrete forming may be ancient, but its evolution is not. There are better ways to design and protect this age-old practice. And now we have a way to avoid puncturing a building’s key line of below-slab protection – the vapor barrier – against formwork penetrations.
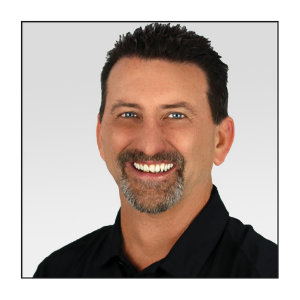
Written by Steve Lutes
Steve Lutes was the National Product Manager for Beast® concrete accessories at Stego Industries, LLC.
- Stego (26)
- StegoCrawl (24)
- Stego-Awareness (17)
- Case Studies (14)
- StegoHome (14)
- StegoCrawl-Consideration (12)
- StegoCrawl-Awareness (11)
- Customer Stories (9)
- Stego-Consideration (9)
- Pango (8)
- Beast (7)
- StegoHome-Awareness (7)
- StegoHome-Consideration (7)
- How to Install (6)
- Drago (5)
- Pango-Awareness (5)
- Beast-Awareness (4)
- Beast-Consideration (3)
- Drago-Awareness (3)
- Pango-Consideration (3)
- Stego IQ (3)
- Drago-Consideration (2)
- StegoCrawl-Decision (2)
Popular Posts
Stay Connected.
Enter your email below.
Post Comments