Quality Vapor Barrier Installation Support Produces Quality Buildings
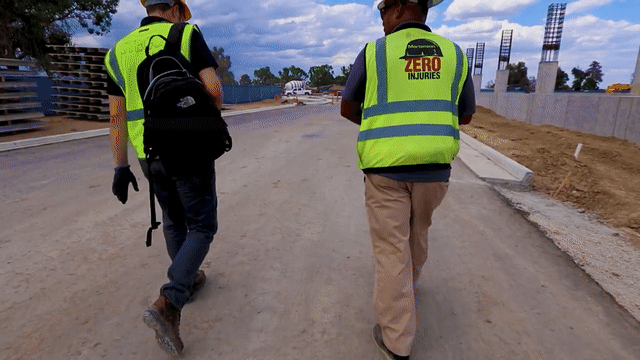
Footage for this video was captured prior to COVID-19 social distancing recommendations for the workplace.
Mortensen Concrete Uses Stego® Installation Support to Multiply Project Team Expertise and Deliver Peace of Mind to its Building Owners
When you are responsible for some of the biggest construction projects in the world, you must always innovate new ways to get your project teams sharing information and lessons learned.
The key to most large, multinational companies and processes is economies of scale. But in construction, if project crews are not talking and sharing expertise with each other, the efficiency is lost; there may be no proportionate saving in costs.
For Mortenson Construction, one way to keep these conversations flowing is by taking advantage of every opportunity to invite their project stakeholders onto their construction sites:
"We want to ask the questions – we want to have everybody come in,” said Mortenson Superintendent Joe Gonzales. “We want to be as transparent as possible so we can share that information across all our projects and other companies as well.
It was for this reason that Stego Industries Regional Manager Tom Marks paid a visit to Gonzales’ job site: the Fitzsimmons Bioscience Parking Garage in Aurora, Colorado.
The Challenge: Sharing Vapor Barrier Installation Best Practices Across a Multinational Construction Firm
Gonzales has been working with Stego® Wrap Vapor Barrier since 2001. He knows the dimensions and weight of every roll and has the details of his project committed to memory, down to the inch.
But one superintendent’s remarkable, encyclopedic memory of below-slab vapor protection cannot be cloned onto every single component of every Mortenson job site without an intentional effort from the entire company.
That’s why Mortenson Quality Control Manager Richard Kee invited Marks to review their vapor barrier installation, which they decided to use even though the project was an open-air parking garage.
“Knowing that you’ve done everything right, up-front, is key to everything else,” Gonzales said. “Teaching the individuals who work under me to do the right thing is really huge, because the next step is they take that to whatever site they’re working on.”
The Solution: Stego Installation Support - Industry Leading Experts Providing Local Installation Support
While Mortenson finds ways to involve any willing stakeholder to participate in their quality assurance program, Stego Industries enthusiastically matches the effort with their Installation Support Program.
When a designer, engineer, contractor or building owner chooses a Stego barrier solution, they gain access to Stego’s network of full-time technical experts across North America.
The program does not begin and end with visits to job sites. Stego’s experts are available from project conception all the way through to final installation. They collaborate with project teams on the best way to protect their slabs from the perils of the below-slab environment, including water vapor and soil gas diffusion. This includes:
- Technical design support
- Full submittal documentation
- Pre-installation conference
- Advanced training for contractors
- Installation review and letter
“The vapor barrier is something that gets buried under concrete; there’s only one chance to do it right,” Marks said. “The design and selection of the below-slab vapor barrier is critical, but we also need to understand the actual installation of the system. That may be equally as important into how effective that system is at ultimately stopping vapor transmission.”
The Solution: Peace of Mind, for Builder and Owner
Mortenson’s robust, company-wide quality assurance program not only fosters an exchange of ideas, it saves them time and money. They can achieve those critical economies of scale even among different crews around the world by taking what they learn on each job site and sharing it within the company.
That starts by understanding the value they get from opening job sites to each stakeholder with expertise to share.
“We all want to think we know it all… but experts are a tool for us to be successful,” Gonzales said. “Our craft members understand the exact installation process without worry.” That peace of mind moves through trades and project teams, but all the way to their clients, the eventual owners of their building projects.
“Our quality assurance and quality control program is one of a kind,” Gonzales said. “When you take all that paperwork back to the owner, they can see all that documentation for themselves, understanding that yes, their project is well-built.”
Stego’s Installation Support program is also unmatched in the industry. Like Mortenson Construction, Stego is proud to offer a level of expertise and service at no-cost, wherever Stego is specified, that lead to the best possible protection of buildings from the below-slab environment.
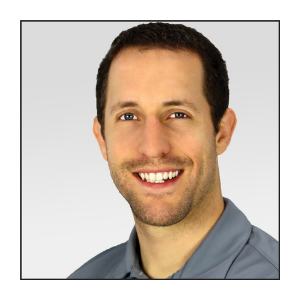
Written by Dan Marks
Dan Marks was the former Technical Director at Stego Industries, LLC.
- Stego (26)
- StegoCrawl (24)
- Stego-Awareness (17)
- Case Studies (14)
- StegoHome (14)
- StegoCrawl-Consideration (12)
- StegoCrawl-Awareness (11)
- Customer Stories (9)
- Stego-Consideration (9)
- Pango (8)
- Beast (7)
- StegoHome-Awareness (7)
- StegoHome-Consideration (7)
- How to Install (6)
- Drago (5)
- Pango-Awareness (5)
- Beast-Awareness (4)
- Beast-Consideration (3)
- Drago-Awareness (3)
- Pango-Consideration (3)
- Stego IQ (3)
- Drago-Consideration (2)
- StegoCrawl-Decision (2)
Popular Posts
Stay Connected.
Enter your email below.
Post Comments