When and Where to Install a Below-Slab Vapor Barrier
7 Factors to Consider When it Comes to Under-Slab Vapor Barrier Placement
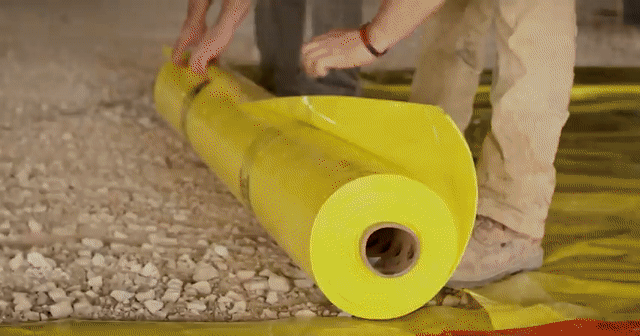
Throughout Stego’s years of experience in the industry, we’ve had countless conversations with architects, designers, and builders about the critical role of under-slab vapor barriers in construction. A frequent question we encounter centers on placement: when and where to install below-slab vapor barriers for effective protection.
Download the Guide Now: Vapor Barrier Placement Tips
This article draws on insights developed over years of working with industry experts to help the construction industry make informed decisions about vapor barrier placement and the key factors that can influence the design plans.
When to Place a Below-Slab Vapor Barrier: Three Easy Steps to Get Value
Building conditions that dictate when to use a below-slab vapor barrier.
After decades of study, the American Concrete Institute (ACI) has clear guidance on when you should use a below-slab vapor barrier. I like to boil them down to this:
1. Will the slab have moisture-sensitive floor coverings, coatings, or goods?
These are, according to ACI Committee 302: Sheet rubber, vinyl, VCT, carpet, hardwood, athletic floors, laminates and epoxy. In some cases, those materials are sensitive to moisture themselves. In others, water-based adhesives may be used to secure these floor coverings, which can be degraded by the unwanted reintroduction of moisture.
Another consideration: even if there’s no possibility for a moisture-sensitive floor covering, will there be moisture-sensitive goods stored in contact with the slab? If so, your answer here is also ‘yes,’ as these goods can be degraded or spoiled by moisture vapor diffusing through the slab – accumulating and condensing on their undersides – as well.
2. Will the slab underlie a humidity-controlled area?
One of the basic functions of HVAC systems is to remove humidity from the building envelope. An unprotected slab provides a relatively porous, unimpeded avenue for moisture diffusion into the building envelope, making the job of your HVAC system harder.
3. Will your building project have either #1 or #2 in the future?
If you can answer ‘yes’ to any of the three questions, you should use a high-performance vapor barrier with extremely low permeance and high puncture resistance and tensile strength.
It really is that simple. Other factors that may seem important intuitively (a lot of people ask about the depth of their water table) are not part of the equation:
“There has also been a thought process that below-slab moisture protection is not necessary in drier climates where the water table is well below the building site. Today, many of these mindsets have changed as those who once resisted the use of below-slab vapor protection have come to better understand and respect the science of moisture movement. Others have painfully come to a similar understanding only after being taken to task when an expensive flooring failure has occurred.”’
- Peter Craig, Take the Ground out of Play, 2007
One of the members of ACI who “wrote the book” on the topic has an even easier checklist than Committee 302 developed:
“This author firmly believes that a floor slab is part of the building envelope and that every slab on ground should have a vapor retarder meeting ASTM E1745 installed directly beneath the concrete.”
- Howard Kanare, Why are We Still Having Problems with Moisture and Concrete Floor Slabs? 2007
A below-slab vapor barrier has a permeance rating of less than 0.01 perms to provide exceptional protection against water vapor diffusion. Making sure that vapor barrier meets ASTM E1745 Class A is important as well. To meet Class A specifications, it must also have a minimum tensile strength of 45 lbs/in. and a minimum impact puncture resistance of 2,200 grams, which both demonstrate the membrane’s ability to withstand the construction environment.
Blog Post: What is ASTM E1745? A Beakdown of the Standard and Classification
Where to Locate a Below-Slab Vapor Barrier: Four Factors to Consider When Installing
When it comes to long-term moisture protection within a building, blotter layers can do more harm than good.
From a moisture-protection standpoint, it is my strong belief – reinforced by decades of ACI study and expert opinions – that the under-slab vapor barrier should be located directly below the slab, without the use of a layer of granular fill (sometimes sand) sandwiched between the slab and vapor barrier, often referred to as a “blotter layer.”
Many designers and contractors may believe that a blotter layer can allow the slab to dry more evenly. This is often true, at least initially, but the potential benefit is often outweighed by the associated costs. Each of the four factors I’ve provided below—intended to help project teams select the location of their under-slab vapor barrier—will also explain the many unintended consequences of a blotter layer that their users may not have considered.
1. No two projects are created equal
Every building project has innumerable unique qualities and many stakeholders representing different concerns about its design, from structural engineering to aesthetics. Despite my strong belief that a below-slab vapor barrier should always be located in direct contact with the slab, you should always confer with the designer and engineer of record about how to meet the unique demands of slab design with the overall construction of the building.
2. Waiting a few hours will pay dividends for years
Proponents of blotter layers point to its ability to allow bleed water to leave the bottom of the slab, thereby helping to maintain an expected finishing schedule.
It is true that a slab cast directly over a vapor barrier will not lose moisture to the subbase and all the bleed water will be forced upward. This can lead to a slightly delayed finishing timeline, usually between 30 minutes and 2 hours. Work with your concrete placement team to account for this on their timeline, as it can save you profound headaches in the long-term. The reason? Bleed water that migrates into the blotter layer doesn’t disappear; it is held below the concrete by the vapor barrier and will eventually diffuse back up through your slab. If the floor covering has been placed before the blotter layer can sufficiently dry, which is often the case, then you’ve just exposed it to an unwanted moisture source that could cause a failure.
3. Addressing potential moisture gradients
Some reports, citing an increased moisture gradient that develops within the slab, blame placing a slab directly on a vapor barrier for increased plastic shrinkage cracking. This, however, tends to be a function of the concrete mix’s shrinkage potential, curing techniques and ambient conditions. A moisture gradient that develops within an early slab can also lead to warping (what we tend to call “curling”). This affect is manageable, and the cost to address/minimize initial curling is much less than fixing the moisture issues associated with a blotter layer (or lack of a vapor barrier altogether) mentioned above. In both cases, appropriately specifying and working with your placement team on proper mix design and concreting practices should mitigate against cracking and curling.
Video: Get a 3-minute overview of the hard facts about concrete slab curl in this Stego IQ episode.
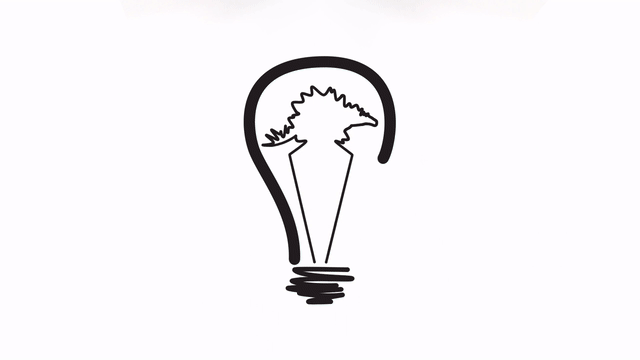
4. What will construction conditions be like?
In some cases, designers opt to use a blotter layer to add a cushion to protect the membrane during the slab placement and its hardware, like rebar and other formwork. Too often, this practice is a holdover from the days of generic 6-mil polyethylene sheeting that could not withstand the wear and tear of slab placement.
21st Century high-performance vapor barriers are carefully engineered with slab placement in mind. (“Cushion” layers placed below the vapor barrier and over a properly compacted subbase are often unnecessary for the same reason). What’s worse, a blotter layer will obstruct the view of any possibly damaged areas of the vapor barrier. Should water migrate through a damaged area, the blotter layer provides an avenue for it to spread out across the entire underside of the slab.
Let's Keep the Conversation Going
These two checklists and the vapor barrier placement flowchart above usually cover the concerns we have in conversations with designers who haven’t spent their time thinking about under-slab vapor barriers. Keeping these 7 tips in mind during the design phase can protect their foundation for the life of their building, to say nothing of keeping their project on schedule.
We love these conversations that dive into the details on below-slab vapor protection, and we’re here to help guide the construction community through the process every step of the way.
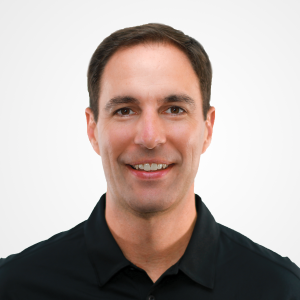
Written by Page Cotton
Page Cotton is the National Product Manager for Drago Wrap and Stego Wrap. Since 2005, he has had experience educating the industry about the effects of the below-slab environment on building health and its inhabitants. Page enjoys working as a trusted consultant to architects, engineers, and contractors to further their understanding of sub-slab barrier systems.
- Stego (26)
- StegoCrawl (24)
- Stego-Awareness (17)
- Case Studies (14)
- StegoHome (14)
- StegoCrawl-Consideration (12)
- StegoCrawl-Awareness (11)
- Customer Stories (9)
- Stego-Consideration (9)
- Pango (8)
- Beast (7)
- StegoHome-Awareness (7)
- StegoHome-Consideration (7)
- How to Install (6)
- Drago (5)
- Pango-Awareness (5)
- Beast-Awareness (4)
- Beast-Consideration (3)
- Drago-Awareness (3)
- Pango-Consideration (3)
- Stego IQ (3)
- Drago-Consideration (2)
- StegoCrawl-Decision (2)
Popular Posts
Stay Connected.
Enter your email below.
Post Comments