Which Water Vapor Permeance Test Should You Use? ASTM E96 or ASTM F1249
5 Key Differences of These Permeance/WVTR Test Methods for Under-Slab Vapor Barriers Explained
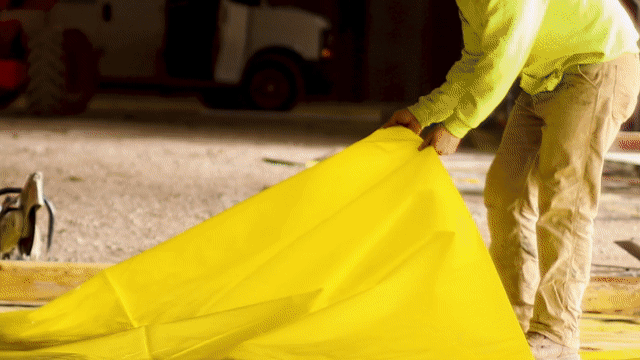
What if I asked you to measure the thickness of a dime? Which tool would you use to measure, a ruler or a set of digital calipers?
Both tools would give a measurement. One (digital calipers) would be highly sensitive, engineered for precision readings of thickness; the other (ruler) may be fairly accurate (it would get you in the ballpark if you have a good eye) but would be extremely difficult to repeat and reproduce.
You could say the same thing about two different tools to measure the permeance of a below-slab vapor barrier on your construction project.
ASTM E1643 provides important requirements, that contractors and architects alike should consider when specifying and/or installing under-slab vapor retarder systems.
How well the components of our building envelope resist the diffusion of water vapor is important. Place an impermeable material where you need a semi-permeable one, or vice versa, and you may find yourself with unwanted condensation. With unwanted condensation in a building comes the increased potential for mold growth, aesthetic issues, or even (eventually) structural damage, which can further imply liability issues, operational interruption costs, and so on.
Designing and constructing an effective building envelope—one that properly and adequately deals with moisture—depends, then, on appropriately locating the right materials. Very (very) knowledgeable individuals have written volumes on how to sequence envelope components/layers in relation to one another: air barriers, vapor barriers, insulation, etc. We always defer to those experts.
But how to quantify the ability of a product/material to resist water vapor diffusion?
If you’ve read even a handful of data sheets that cite this attribute, you’ve no doubt seen references to different test methods and different units. Two standard test methods are most common: ASTM F1249 (“F1249”) Standard Test Method for Water Vapor Transmission Rate Through Plastic Film and Sheeting Using a Modulated Infrared Sensor and ASTM E96 (“E96”) Standard Test Methods for Gravimetric Determination of Water Vapor Transmission of Materials
So, how do these test methods work and what do they tell us?
Let’s dive into each with the aim of identifying five important differences—and two critical similarities— that matter when selecting and comparing products for your building project.
Similarity #1 Both ASTM F1249 & E96 Are Intended to Measure Water Vapor Transmission
Both F1249 and E96 are designed and intended to measure the same thing: the amount of water vapor that passes through a section of a product over a period of time, based on a differential in partial water vapor pressure on either side. We call this a product’s “permeance rating” and express it (in the US) as:
mass [grains (1 grain = 1/7000 lbs)] per area [square feet] per time [hours] per partial pressure difference [inches of mercury]
You are likely to see it simplified on a data sheet like this: US Perms = gr/(ft2*hr*in-Hg)
A product’s permeance rating can change based on certain conditions—saturation of the sample, and ambient RH and temperature, primarily—but those factors notwithstanding, testing per E96 and F1249 should, in theory, produce the same result. But in the real world, they tend not to do so, and it’s critical to understand why.
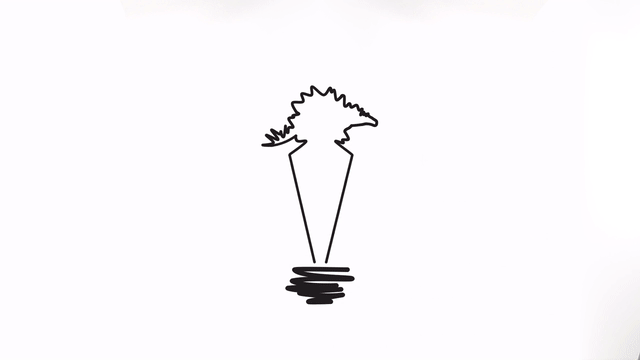
NOTE: A product’s water vapor transmission rate (WVTR) is measured and quantified in the same way as the permeance rating, except that WVTR leaves out the partial vapor pressure difference (units are often simply [gr/(ft2*hr]). Unless the test method used and conditions of the test are specified (at least the temperature and RH difference), the WVTR of a product doesn’t necessarily provide comparable data between products the same way a permeance rating does.
Difference #1 Methodology – Measurement & Equipment
In the simplest, most misleading terms (we’ll put you back on track shortly), E96 measures a (change in) mass, and F1249 measures an electric signal (voltage). Huh? Let’s start with E96.
E96 is often referred to as the gravimetric (think weight) or “cup” method for good reason. Here’s what E96 looks like:
- E96 separates the contents of a test cup from a test chamber with the product under evaluation. The contents of the cup dictate the relative humidity on the side of the product it encloses, and the chamber controls the system temperature and “external” (external to the cup) relative humidity.
- The operative measuring device used in E96 is a scale—as water vapor migrates into or out of the cup (more on this below), it records the change in mass. We run the test until the rate at which the mass is changing becomes steady, and we then simply divide this change in mass by the area of the specimen, the time over which the mass change was recorded, and the difference in partial vapor pressure across the specimen based on the temperature and relative humidities at play. Et voilà—we have the product’s permeance rating.
F1249 adds an extra step to this process. Here’s what F1249 looks like:
- The test “chamber” is housed in a specialized machine wherein the test specimen separates a moisture source of constant relative humidity (usually 50% or 100%) from the flow of ultra-high purity nitrogen gas. As water vapor diffuses across the membrane, it is “picked up” by the gas and run across a pressure-modulated infrared sensor. The amplitude of the signal spit out by the sensor is proportional to the amount of water vapor present, and the machine’s accompanying software package can read it, factor in the relevant specimen parameters, and determine the WVTR and/or permeance rating.
- Due to this extra step, these machines require calibration: a specimen with a known permeance rating is tested, and the resultant voltage is related to this known value by way of a calibration factor.
In this way, E96 can be said to be a more “direct” method, although, for reasons we’ll discuss in Difference #3, this may be more a bug than a feature.
Difference #2 Methodology – Relative Humidities
E96 uses three main scenarios in testing: “dry cup”, “wet cup”, and “inverted wet cup”. They intuitively betray their respective setups:
- The “dry cup” method involves utilizing a desiccant within the test cup and maintaining 50% RH in the ambient chamber. Water vapor is expected to diffuse into the cup (i.e., the cup’s mass will increase over time), and the mass recorded is essentially the water vapor absorbed by the desiccant.
- The “wet cup” method replaces the desiccant with water, creating a 100% RH environment inside. The chamber is maintained at 50% RH again, and thus water vapor is expected to diffuse from the cup into the chamber (the mass of the cup will decrease over time).
- In the third “inverted wet cup” scenario, the cup is turned upside down so that the liquid water is in contact with the test specimen.
NOTE: Alterations can—and likely should— be made to the conditions cited above if those conditions will better match the actual application of the products being tested. We’ll discuss this further below, and we’ll talk about where/when this adjustment matters.
With F1249, many of the machines allow control of the relative humidity on the challenge side, the side from which water vapor will migrate. 50% is a commonly selected relative humidity for testing, as is 100%, which can be easily created by wetting a sponge and placing it adjacent to the specimen, opposite the side over which nitrogen gas is run. However, unless special setups are created, the side to which water vapor migrates—into the nitrogen—will always have a relative humidity of 0%. This often doesn’t matter, but in some cases, it can, as we’ll see in Difference #4.
Difference #3 Methodology – Speed & Sensitivity
Aside from the equipment involved, how long these test methods run represents the biggest difference between them. This disparity is a function of how the mass of water vapor moving across the test specimens is calculated, and the sensitivity of the equipment in service.
Remember that E96 uses a scale to record mass changes over time. But how quickly will the mass change with a specimen whose permeance rating is quite low? At least for under-slab vapor barriers, with a permeance rating of 0.01 perms or less, the answer is: not very quickly.
This is not a problem if we have sufficiently sensitive equipment and/or can run the test for a sufficiently long period of time. Doing the latter allows enough mass to pass through to drown out any noise in the data or error naturally occurring in any of the equipment (or that might creep in due to opening and closing the chamber, which temporarily alters chamber RH and temperature and thus can affect results). Typically, for E96, in order to achieve a steady-state condition, where the rate of mass transfer across the test specimen evens out, this means running tests for days or weeks (sometimes longer).
F1249 uses a different method—signal conversion via a pressure-modulated infrared sensor—which has proven to produce repeatable, reproducible results in often a period of hours to days. The increased speed is a function of the high sensitivity of the equipment. Sensitivity is not as critical in equipment for products that are designed to be more breathable and allow a significant amount of moisture through, like many above-grade air barriers; both E96 and F1249, in such conditions, the test will detect a sufficiently large amount of water vapor in the period of a day or so to register meaningful results.
However, with better barriers—like high-performance under-slab vapor barriers—only F1249 equipment has proven sensitive enough to complete testing quickly. According to one of the leading manufacturers of F1249 equipment, to compete with their models (which can detect down to one part per million of water vapor), the equivalent resolution needed for gravimetric (weight/mass) measurements per E96, across a 50-cm2 sample, would be on the order of magnitude of 0.000025 grams. In other words, the scale would need to be able to pick up on changes in mass, over the course of a day, equal to the weight of a small fraction of the mass of a grain of sand.
Think of it this way: if you are tasked to measure the mass of an elephant, whether or not your device gives readings rounded to the nearest kilogram or the nearest milligram doesn’t really matter; if the first device "misses” a few fractions of a kilogram, the “error” is still quite small compared to the value you are measuring. But measure the mass of the gold ring you are pawning (presumably to buy some better measuring equipment) and registering to the nearest kilogram won’t cut it.
If you have studied certain kinds of statistical analysis, you recognize these terms used above: “repeatable” and “reproducible.” You’ll have anticipated our current differentiator, which may be the most important of them all, and which is our final difference to cite: precision.
Difference #4 Precision
ASTM International studies many of the test methods under their umbrella to determine how close test results are to one another when obtained in the same lab and at multiple labs. The former refers to repeatability, and the latter refers to reproducibility. If a test method is found to be highly repeatable, then we would expect only relatively small differences between test results when recorded by the same operator, using the same lab/conditions, and on the same equipment over short time intervals. Repeatability for both E96 and F1249 is fairly good and can be studied more in the “Precision and Bias” sections of each standard.
Reproducibility is “harder” to achieve. High reproducibility indicates that we would expect relatively small differences between two test results when recorded by disparate labs with different operators and equipment. It is in this regard that F1249 excels over E96. The statistical analysis involved here gets complicated quickly, but what conceptually drives this home are two advantages F1249 maintains over E96:
- Precision is closely tied to sensitivity, and F1249 typically involves equipment capable of greater sensitivity.
- F1249 takes many operator-dependent variables out of play (how well specimens are sealed, opening chambers during testing, etc.) that can contribute to imprecision.
Underlying both precision and sensitivity is the idea of accuracy as well. We want test equipment that:
- is sensitive to small inputs (necessary when dealing with small changes in mass);
- delivers precise results, in so far as they are repeatable and reproducible; and
- delivers accurate results—reflective of the actual permeance rating of the products we are testing.
These are all tied together, and F1249 allows for more sensitive equipment, objectively more precise execution of the test method, and these advantages tend to lead to more accurate results.
Difference #5 Applications
We’ve already alluded to this fact, but it is worth noting that low-permeance materials are most often better served by the use of F1249, the same way the value of your gold ring is better served by a more sensitive scale. If both F1249 and E96 are run “properly” and “perfectly” they will yield, theoretically, the same result. In practice, we can see now why this may not happen. So, when is E96 a “better” test?
The answer lies in the answer to two related questions:
- is the product’s permeance rating affected by its surroundings (e.g., RH) and,
- if yes, when (that is, in what eventual applications) can E96 better reflect the in-service conditions that will surround the product?
For under-slab vapor barriers (which are primarily polyethylene in composition), the permeance rating is not heavily affected by ambient RH or even the presence of liquid water against one side of the membrane. These also tend to be very low-permeance products (the good ones at least critical to protecting low-permeance flooring materials). Thus, F1249 is a better choice.
However, some materials’ permeance ratings are greatly affected by the ambient RH. Certain “smart” vapor barriers are impermeable at lower (average) RH and become semi-permeable as RH increases. This can be a major advantage in above-grade applications, especially in exterior walls where the permeance of certain control layers may need to be lower to reduce vapor diffusion in certain conditions/time but more permeable in other times to help facilitate drying in the right directions.
The average relative humidity for F1249 is typically 25% or 50% (0% on one side, 50% or 100% on the other). It can be no higher than 50% when nitrogen is used as the carrier gas. However, E96 allows for higher relative humidity averages. In the wet cup method, one side is 100% and the other is typically kept at 50%, yielding an average of 75%. Many “smart” materials have a permeance that increases quickly after the average RH passes 75%. For these materials, which also tend to have a much higher permeance rating than under-slab vapor barriers, E96 is a “better” choice.
Similarity #2 - Both Test Methods are Accepted by ASTM E1745
Despite their differences, E96 and F1249 are both useful test methods. Because F1249 is objectively more precise, it is the standard we (Stego Industries) have opted to use to test our under-slab vapor barrier and retarder products.
The other (main) reason why we use F1249? ASTM E1745 accepts it.
Likely because E96 is more often cited and used heavily in above-grade applications, E96 tends to make its way into more specifications. E96 is also useful for some wet-applied vapor-proofing accessories (e.g., mastics) however, for under-slab vapor barriers, ASTM E1745 Standard Specification for Water Vapor Transmission of Materials or Granular Fill Under Concrete, cites both as acceptable.
Any specifier that requires a manufacturer to provide their product’s permeance rating per E96 should also accept that result when tested per F1249, at least for under-slab vapor barriers, where average relative humidity across the sample does not tend to affect the results. There is in fact a growing sense that E96 could/should be phased out of E1745, but that’s a whole other article entirely.
The Preferred Test Method for Under-Slab Vapor Barriers
I often think about measuring the thickness of that dime. Would you use a ruler or a pair of digital calipers? I’d use the calipers every time. When it comes to testing under-slab vapor barriers for their water vapor permeance rating, F1249 is an ideal choice and should be accepted in place of E96.
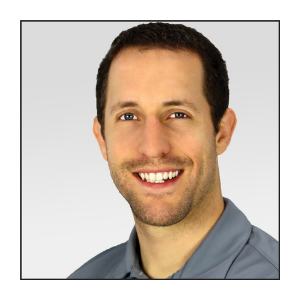
Written by Dan Marks
Dan Marks was the former Technical Director at Stego Industries, LLC.
- Stego (26)
- StegoCrawl (24)
- Stego-Awareness (17)
- Case Studies (14)
- StegoHome (14)
- StegoCrawl-Consideration (12)
- StegoCrawl-Awareness (11)
- Customer Stories (9)
- Stego-Consideration (9)
- Pango (8)
- Beast (7)
- StegoHome-Awareness (7)
- StegoHome-Consideration (7)
- How to Install (6)
- Drago (5)
- Pango-Awareness (5)
- Beast-Awareness (4)
- Beast-Consideration (3)
- Drago-Awareness (3)
- Pango-Consideration (3)
- Stego IQ (3)
- Drago-Consideration (2)
- StegoCrawl-Decision (2)
Popular Posts
Stay Connected.
Enter your email below.
Post Comments