No Floor Covering? 4 Reasons Your Slab May Still Need a Vapor Barrier
Consider Adding a Layer of Protection for Your Resilient Building Design With an Under-Slab Vapor Barrier—You May Be Very Glad You Did.
The utility of under-slab vapor barriers in applications where a concrete floor slab will receive moisture-sensitive coverings or coatings is hopefully all too clear for the design and construction communities.
Accumulated water vapor is the bane of these systems, and unfortunately vapor is ubiquitous beneath almost all slabs on ground. Without proper vapor protection, the water vapor that was once directly below your concrete will find its way directly below your flooring, bringing with it the potential for adverse impacts on those coverings, their adhesives, and your pocketbook.
What are the common threads in the scenario described above?
One is obviously water vapor, but the other you may identify is the floor covering or coating. We know how to take the ground—and the water vapor it holds—out of play: we do so with an under-slab vapor barrier.
But if your slab system has no floor covering, does the vapor barrier do anything for you? Said another way: “Do I need a vapor barrier if my slab will remain exposed?”
#1 The Building’s Intended Use May Change Over Time
One obvious consideration is that the sentiment “will receive [a floor covering]” is a temporally open-ended statement, with the operative word being “will.” Many slabs are designed with an initial application in mind that may change over the course of the life of the building, either due to updated needs of the building’s owner, a change of building ownership, and/or other unanticipated considerations.
This may mean that a slab whose surface is originally expected to be exposed will receive a covering later. If no under-slab vapor barrier is in place, methods to protect the subsequently installed floor coverings are numerous, but often an order of magnitude (or two) more expensive to implement (this is a niche of the industry where we hear time and time again that “you get what you pay for.”) Take a look at our Topping Slabs eBook for more information on topical mitigation systems.
#2 Material or Merchandise May Be Damaged as Moisture Accumulates Beneath
If you know the slab will never receive a floor covering—or you’re comfortable leaving that problem for a future owner to consider—fair enough.
But let’s think back for a moment and envision an abundance of water vapor migrating through a slab on ground. It will do so via vapor drive, in which the water vapor pressure in the high-relative humidity soil will move via diffusion into the (relatively) lower water vapor pressure environment of the interior space.
Cap the slab and that water vapor will build up below the cap, and issues may ensue. Does that “cap” need to be a floor covering? In fact, it doesn’t—much to the chagrin of many a warehouse owner or tenant.
Any relatively impermeable material can act just like a resilient flooring material:
- area mats,
- equipment, and
- many different types of inventory.
We've seen and heard of many cases of cardboard storage boxes and/or merchandise itself being damaged as moisture accumulated beneath, condensed against, and soaked into, various items stored across the warehouse’s floor.
To add insult to injury, if that inventory is moved and the accumulated, condensed (liquid) water is left to evaporate, it can leave behind concrete efflorescence. This is that chalky white substance often seen on retaining walls and warehouse floors and is the result of alkaline salts from the surface of the slab being dissolved into solution by water condensate and then concentrated and deposited on the surface as the water evaporates.
Concrete efflorescence can be an eye sore in the best cases, and, in the worst, can contribute to sweating slab syndrome, an unwelcome phenomenon with several causes, one of them being an excess of these hygroscopic alkaline salt residuals that attract humidity from the atmosphere and deposit them on the surface. It can be a slippery, dangerous mess to deal with. So, if your slab will always be exposed, and your inventory always elevated, are you out of the woods?
Maybe, but again we need to consider the water vapor moving through the slab and what else it can affect. It may not seem like it would be a lot of moisture diffusing through the slab at any given time—depending on any number of factors and your definition of “a lot”—but any additional water vapor in your building interior can be a burden.
This is highlighted especially well in applications where humidity and/or temperature controls are active, and further where both are kept low. Not only does this combo increase the strength of vapor drive of water vapor into your building, but any “excess” water vapor in the building now leads to “wasted” energy consumed by the HVAC system to remove that water and/or change its phase and temperature in the cooling process. Cold-storage facilities, for this very reason, always get a vapor barrier (along with strategically placed insulation, and lots of it).
Whenever one of the conditions or considerations mentioned above applies to a project, the American Concrete Institute Committee 302 has clearly stated a need for an under-slab vapor barrier. In their ACI 302.1R-15 Guide to Concrete Floor and Slab Construction, they have published a flow chart describing exactly this.
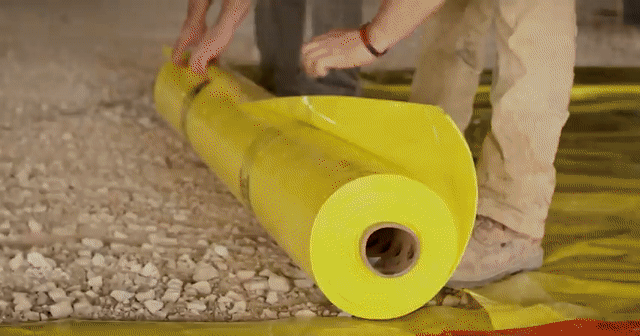
#3 Are Soil Contaminants, Methane, or Radon a Concern?
One last consideration for the utility of under-slab vapor barriers should be kept in mind when evaluating a project that may not use a floor covering, and that is the fact that an under-slab water vapor barrier oftentimes can also serve as a soil-gas retarder.
In applications where soil contaminants, methane, or radon are permeants of concern, and/or where creating an air barrier system below your slab is desired, a properly installed vapor barrier specifically intended to impede these harmful gases is often a critical upgrade from water vapor barriers and can be a key component of your mitigation system. Cutting off advective air flow, and the water vapor and these other unwanted soil gases it carries, is an important step in maintaining indoor air quality.
#4 Resell or Future Lease Value
Just because the building was designed to have exposed slabs doesn’t mean it will always have this open system in the future. The flexibility and extensibility of future facility functionality can be valuable from a real estate standpoint. Why would you want to limit the future tenant or buyer pool when choosing to protect the first side of your building?
So, Is a Vapor Barrier Really Necessary?
No floor covering? An under-slab vapor barrier may still be necessary.
There are very few instances, if any, where the migration of unchecked under-slab moisture, or other soil gases, would be considered desirable, so it almost always makes sense to consider adding this layer of protection—you may be very glad you did. Taking a step back to consider the future of your building can help you make the best decisions to ensure a resilient building design.
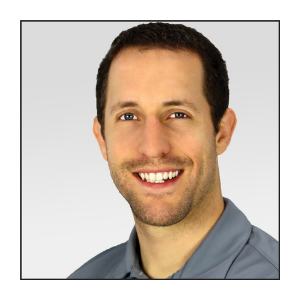
Written by Dan Marks
Dan Marks was the former Technical Director at Stego Industries, LLC.
- Stego (26)
- StegoCrawl (24)
- Stego-Awareness (17)
- Case Studies (14)
- StegoHome (14)
- StegoCrawl-Consideration (12)
- StegoCrawl-Awareness (11)
- Customer Stories (9)
- Stego-Consideration (9)
- Pango (8)
- Beast (7)
- StegoHome-Awareness (7)
- StegoHome-Consideration (7)
- How to Install (6)
- Drago (5)
- Pango-Awareness (5)
- Beast-Awareness (4)
- Beast-Consideration (3)
- Drago-Awareness (3)
- Pango-Consideration (3)
- Stego IQ (3)
- Drago-Consideration (2)
- StegoCrawl-Decision (2)
Popular Posts
Stay Connected.
Enter your email below.
Post Comments