Curling and Warping of Concrete Slabs - 5 Facts You Should Know
A Narrative History of the Biggest Myth around Under-Slab Vapor Barriers
There’s no more common question I’m confronted with than this one:
Contractor: Won’t a vapor barrier or retarder make my slab curl?
Answer: Not as bad as your slab will curl without a vapor barrier or retarder!
This is an easy answer. The benefits to protecting your slab from water vapor with a low-permeance vapor barrier are clear. Water vapor diffusion is not only destructive to moisture-sensitive floor coverings but uninhibited water vapor diffusion – when left unchecked in the absence of a durable plastic membrane below the slab – also greatly contributes to long-term warping of the slab.
The short answer is really that simple. This conclusion isn’t new – there has been little debate among the leading voices in the concrete industry about this issue for years, thanks to their work studying the science of slab curl over the past several decades.
So why is this still among the most common question I get? The misconception around slab curl and vapor barriers is a much longer story – nearly fifty years of research, changing standards, evolving practices and our industry’s strong tradition of on-the-job training among tradesmen. Scientific research, review of industry standards and workforce training happen in distinctly different places and on very different schedules – and that process continues in some corners of our industry even today.
This article intends to resolve that story: the positives and the negatives, the history, the debate and the resolution of this issue among concrete’s standard-bearers.
Get a 3-minute overview of the hard facts about concrete slab curl in this Stego IQ episode.
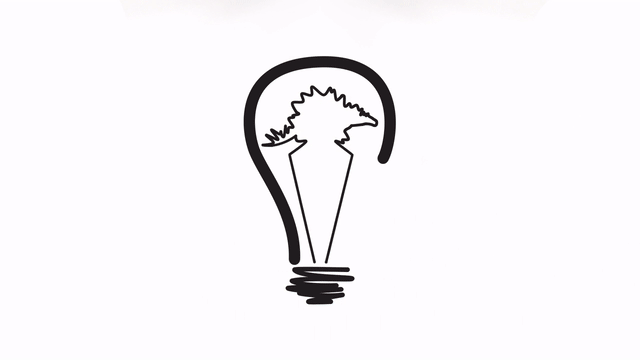
Concrete Warping (You Mean Curling, Right?)
Which one is it: curling or warping? The common term used on the job site is “curling.” When a moisture gradient (as opposed to a temperature gradient) is the underlying cause, the technical term for the phenomenon is “warping.” While there are some technical differences between the terms, their impacts are very similar. For this reason, I will use “curling” and “warping” interchangeably, as do many others.
Concrete curling, according to a leading expert in the industry, is also termed "warping" and is:
“…the upward deformation of the slab at cracks or joints due to the development of a temperature and/or moisture gradient through the depth of the concrete after slab placement.” - Scott Tarr, Concrete International, September 2016
How this moisture gradient develops in the slab is the key to unlocking the entire debate about slab curl and vapor barriers.
These five facts not only tell the story of the debate; they can help you design a better slab with less warping while explaining the scientific conclusions reached by the top slab designers in our industry.
Fact #1: Throw Out Those Outdated Reports
A real forensic accounting of the vapor barrier/slab curl myth might start in 1976, with a study published in ACI Journal Proceedings, which evaluated several construction techniques “and their influence on cracking of concrete in-place and its effect on strength development.”
What did they find? Polyethylene sheeting contributed to cracking in the slab. From my 21st Century hindsight view of the study, I have the benefit of much better technology and practices to cite a myriad of problems with their methodology.
For one, the study set out to evaluate one thing – cracking – but ended up commenting on an issue they did not even evaluate: warping. And yet, in 1980, ACI Committee 302 saw fit to add this to their updated standard on the construction of concrete floors:
“Impervious vapor barriers under the concrete particularly aggravate plastic and shrinkage cracking (and slab curling) … vapor barriers should be avoided wherever groundwater and soil conditions permit." - ACI 302.1R-80, Section 8.4
The finding of this study – and the 1980 revision to the standard – remains today the single biggest contributor to a concrete contractor’s reasoning to avoid the use of a vapor barrier. A present-day review of this 1976 study on concrete cracking would indicate that the researchers observed plastic shrinkage cracking and shrinkage cracking as a result of short-term warping when their test slabs cracked, even though their study did not specifically evaluate for the latter phenomenon.
A half-century later, this finding remains true: short-term slab curl can often be attributed to a vapor barrier. This is the “harm” in the inherent equation that a vapor barrier does “more good than harm” when it comes to warping of the slab.
How does it happen? Differential drying. A vapor barrier does not allow bleed water (or any water of convenience) to absorb into the subbase or grade. This means the moisture in drying concrete is going to leave essentially only from the top, causing the slab to shrink faster (concrete shrinks as it dries) on the top than the bottom, and curl upward in the process.
Differential drying can be exacerbated by adverse ambient conditions. Indeed, the 1976 researchers indicated their test slabs were placed on a “hot and windy day” in the arid Southern California climate. In these conditions, when no vapor barrier is present, the slab at least has a chance to compensate for this by permitting some moisture to move downward, which is likely why the researchers saw more cracking in the test slabs using polyethylene sheeting.
For nearly a quarter-century, this was the beginning and end of the conversation. Vapor barriers were a nuisance and a contributor to cracking and slab curl. How can you blame the contractor for avoiding their use?
The subsequent tips in this article continue our story of how this myth was dispelled and standards were improved. But this “origin story” has a powerful lesson for any best practice in construction: it’s one thing to be “old school” where standards and research have not evolved. But when a standard has been revised and improved many times over the decades, don’t you think it’s time to dust off that 1980 edition of ACI 302.1 and throw it into the recycling bin?
Fact #2: Blotter Layers Only Make Things Worse
Just as the committee recommended to contractors in 1980 to avoid the use of a vapor barrier, they exacerbated other problems with their recommendation of using a blotter layer.
Initial guidance in the 1980 revision called for a three-inch layer of dampened sand or cement-treated sand mixture between the vapor barrier and the slab. This would evolve over the next two decades to “drainable fill” in 1989, then “trimmable, compactible granular fill (not sand)” in 1996.
The thinking was the same with each revision: give the slab some room to release moisture downward upon placement to avoid cracking and short-term curling.
The unintended consequences of this guidance only led to vapor barriers being viewed as the culprit again: while the blotter layer may have temporarily provided room for the slab to dry downward, where was all that moisture ultimately to go? On a long enough timeline – with a vapor barrier taking the ground out of play – the only direction was back up through the slab.
And thus, the blotter “solution” was only a short-term remedy to cracking, all while leaving the moisture trapped between the vapor retarder and the slab, creating greater moisture problems. Blotter layers resulted in widespread floor failures, the very thing the vapor barrier was supposed to protect against:
“In some cases, it turned out that the fill course had taken on a considerable amount of water from rainfall prior to, or during the slab placement. In other cases, it was determined that tears, punctures or improperly sealed penetrations had provided an avenue for moisture to enter the fill course and travel freely beneath the slab which over time increased the moisture level within the slab.”
- Peter Craig FACI, FICRI, CCSMTT, No Sand Please!
In 2001, ACI Committee 302 updated its standard, removing blotter layers from the guidance and recommending concrete placement directly on top of the vapor barrier.
Nearly two decades later, I still get questions about blotter layers. Most industry experts will tell you not to use them.
Fact #3: What's in the Mix?
For nearly a quarter-century, this view of vapor barriers went largely unchallenged within the industry, even as the cheap polyethylene sheeting used in the 1976 study grew obsolete with the advent of highly engineered, cost-effective polyolefin vapor retarders in the late 1990’s.
After removing the blotter layer issue and its negative impacts on flooring failures, in 2004 ACI Committee 302 set out to understand the relationship between the many other variables in slab design, placement and warping. One of the task group’s principal findings as relayed by a member:
“In our experience, curling is related to the concrete mixture paste content and is not a result of the vapor retarder.”
Howard Kanare made similar conclusions in his 2005 book, Concrete Floors and Moisture for the Portland Cement Association, citing the control of the slab’s shrinkage potential of the concrete mix as a method for minimizing curling. The cement paste is what shrinks as concrete hydrates and dries; so, reduce the amount of cement paste—made up of cement and water—and you reduce curling. These findings were additionally supported by the 2008 Portland Cement Association book, Concrete Floors on Ground by Scott M. Tarr and James A. Farney.
In its 11-point checklist to minimize slab curling, The National Ready Mixed Concrete Association (NRMCA) prioritizes concrete mixture as well:
- Use the lowest practical water content in the concrete
- Use the largest practical maximum size aggregate and/or
- Avoid a higher than necessary cement content
Twenty-eight years after the 1976 study on concrete cracking, the ACI Committee 302's task group had undone, corrected or improved nearly every finding in the original study.
On the issue of curling and warping, the standard practices for slab design, vapor barrier installation and concrete placement have remained remarkably consistent ever since. Best practices and tradecraft in the day-to-day grind on the job site, however, are still catching up.
Fact #4: Long-Term Warping is the Bigger Problem
The quick-fixes to plastic shrinkage cracks and short-term curl ultimately contribute more moisture to the slab:
- A wet blotter layer provides a reservoir and/or horizontal pathway for moisture to continuously move upward into the concrete
- Avoiding the use of a low-permeance vapor barrier provides an endless source of new water vapor moving upward from the water table
In the latter case, that moisture gradient in the slab may never be resolved. The humid sub-slab environment keeps the bottom of the slab much wetter than the interior-facing top of the slab. The slab continues to warp. This is the problem of long-term warping.
The difference between what we have called “short-term warping” and “long-term warping” lies in the timing and magnitude of the effect. Slabs cast on a vapor barrier that may have experienced short-term warping will eventually dry fully throughout or the moisture within will equalize across the elevation of the slab, lessening the moisture gradient and lowering the amount of warping into the future. Short-term curling therefore tends to stabilize over time. In the right (or wrong) ambient conditions, where the slab remains wet at the bottom without a vapor barrier and the top of the slab equalizes to dry ambient conditions, long term warping may increase over time. Long-term warping is much more expensive and difficult to resolve than the cost and installation of a highly durable, low-permeance vapor barrier.
This is where below-slab vapor barriers fundamentally do “more good than harm.” There are other ways to protect against short term curling that can come from the temporary moisture gradient seen in slabs protected by a vapor barrier. We’ll get to that next.
In a vapor barrier, there is no better solution to the long-term curling problem: only it can eliminate the long-term moisture gradient that exists below every slab, in every climate.
Fact #5: Adjust Placement and Finishing Options and Slab Curl Will Not Be an Issue
If we accept that vapor barriers make some contribution to short-term warping but can help to eliminate the bigger problem of long-term warping, what can we do to mitigate in the short-term?
Concrete mixture, in Fact #3, is essential. But proper engineering placement and finishing techniques can do the rest. The NRMCA recommends several techniques, none of which are silver bullets alone but which can aggregate into an effective strategy, and all of which should be directed by a qualified professional:
- Proper and thorough concrete curing, including joints and edges
- Joint spacing that does not exceed 24 times the thickness of the slab
- Proper design and placement of slab reinforcement
- Increasing the thickness of the slab at the edges can also help
Tarr also reminds concrete finishers that slabs protected by vapor barriers experience higher bleed and to “adjust finishing timing and procedures accordingly”
There are innumerable techniques, products and methods the best slab designers and placement teams use to keep their floors flat with minimal joint deflection. In an ACI-supported article, The Floor Flatness Report, Mark Cheek defines Floor Flatness (FF), “The FF number is an indication of how bumpy or wavy the slab surface is, demonstrating the quality of the initial strike off and finishing process.” Curling is the bane of floor flatness. The imperative around slab flatness on high-performance floors and for the use of robotics grows with every passing year. Every contractor, designer and building owner understands the economics of “short money.” Don’t opt for the quick-fixes that can create long-term problems!
The End of the Debate, but not the Story
While the debate may have ended around the issue of vapor barriers and slab curl many years ago, there will not be a resolution to this story until widespread acceptance of these practices takes hold.
Understandably, the concrete industry is a vocation where there is no substitute for on-the-job training and know-how. The downside of this tradition, however, means old habits can die hard, sustaining the powerful myth that a vapor barrier will cause your slab to curl.
I’ll know the myth has finally died when I stop getting asked the question.
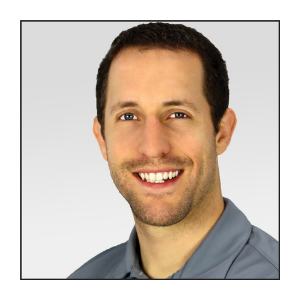
Written by Dan Marks
Dan Marks was the former Technical Director at Stego Industries, LLC.
- Stego (26)
- StegoCrawl (24)
- Stego-Awareness (17)
- Case Studies (14)
- StegoHome (14)
- StegoCrawl-Consideration (12)
- StegoCrawl-Awareness (11)
- Customer Stories (9)
- Stego-Consideration (9)
- Pango (8)
- Beast (7)
- StegoHome-Awareness (7)
- StegoHome-Consideration (7)
- How to Install (6)
- Drago (5)
- Pango-Awareness (5)
- Beast-Awareness (4)
- Beast-Consideration (3)
- Drago-Awareness (3)
- Pango-Consideration (3)
- Stego IQ (3)
- Drago-Consideration (2)
- StegoCrawl-Decision (2)
Popular Posts
Stay Connected.
Enter your email below.
Post Comments