How to Prepare for a Vapor Intrusion Mitigation System
Time to Install? Here’s an In-Depth Checklist to Guide You Through the Pre-Construction Meeting and Installation Preparation
Designing building projects that employ a vapor intrusion barrier can be some of the most complex tasks environmental engineers pull from their professional acumen. A vapor intrusion barrier is a critical component of an overall mitigation system and is typically used in brownfield projects or on other sites that have more than just water vapor diffusing from below the foundation.
Given this complexity, considerable time and research will go into the products and systems specified to protect the building envelope. This is time well-spent; any vapor intrusion mitigation system needs verified performance and efficacy for the specific project where it will be used. But merely specifying the right system does not ensure success. An experienced project design team – building owners, architects, environmental engineers, and other designers – along with the contractors they employ to install the system can encounter innumerable pitfalls if they haven’t effectively communicated, collaborated, trained, and tested their system to prove a successfully protected building from the contaminants below.
This article provides a four-step checklist to ensure you’ve adequately prepared for a vapor intrusion mitigation system, maximizing your opportunity for an efficient and effective installation that will move your building project forward on time and on budget.
1) Before the Meeting: The Design Plan Groundwork before the Real Groundwork
A strong design plan is critical to every project, particularly when it involves vapor intrusion and/or soil gases that could endanger the occupants/receptors in the building after construction.
As I mentioned, however, identifying the right products and putting them into writing in your design plan is not an impermeable symbol of protection against installation pitfalls.
Just as important in that design plan: the design professional or engineer of record should include in their plan that a pre-construction/slab meeting must take place.
Pre-construction/slab meetings bring the words off the page of a design plan. It’s a chance for the project design team to discuss pitfalls before they happen. It’s also a critical time to evaluate that your installation crew has both the means and the methods to install your vapor intrusion mitigation system properly.
Above all else, by indicating in your design plan that a pre-construction meeting must take place, you’re sending the message to everyone involved in your project that open communication will be vital to your project’s success. This communication and collaboration happening all the way through will help prevent a “bad news” phone call somewhere much farther down the road.
2) The Pre-Construction Meeting: The Five W's (and One 'H') to Ensure Success
When it’s time to have the pre-construction/slab meeting, think like a journalist does, using “The 5 W’s” – who, what, when, where and why. A good journalist will always answer ‘H’ – how – as well. These six bullet points will open those channels of communication and identify obstacles before they present themselves, and even prevent them from happening, in some cases.
- Who should attend? The general contractor, the concrete contractor, the installer of the vapor intrusion mitigation system, the design professional (most likely the environmental engineer behind the design plan), and the manufacturer of the vapor intrusion mitigation system.
- What should be discussed? The building owner’s expectations and objectives. How the submittal and quality assurance review will take place to make sure these expectations and objectives are met.
- When should the installation of the vapor intrusion mitigation system and concrete slab’s placement be scheduled, and how will those schedules depend on other activities on-site? Timing and clear communication are critical components of a successful installation. The general contractor and concrete contractor can also collaborate about the readiness of the building site.
- Where will the system be installed? This provides the environmental engineer the opportunity to identify and address perimeter conditions and other spots in the system that require particular attention and care. A good manufacturer’s representative will be on hand to educate. The general contractor and concrete contractor can chime in with the sub-base type, its preparation, and readiness.
- Why install it this way? While the first four ‘W’s are straightforward, this is where the work of a good pre-construction/slab meeting proves its value. Getting the stakeholders in the same room (or on the same call) turns a building owner’s expectations and objectives into an achievable plan. This is the chance for the installer of the vapor intrusion mitigation system to ask questions of both the manufacturer and the environmental engineer. Helping the installer understand why certain decisions were made, products or accessories are used, and the conditions that must be met to ensure they achieve these objectives.
- How will the installation be done, and how will we measure its success? Are there concrete placement and finishing procedures that are relevant to the vapor intrusion mitigation system, such as the movement of concrete mixers, buggies, or pumps over the system? Will the concrete be laser screeded or hand-screeded, and how might that impact the system? Are there other unique site conditions that must be accounted for? Again, having the manufacturer of the system (who should be experienced and well-versed with other similar installation conditions) on hand to help identify these conditions – and help troubleshoot solutions to potential obstacles – can mean the avoidance of significant pitfalls later.
Most important to the ‘how’ conversation will be measuring its success. Which submittal and quality assurance review procedures will be in place?
The collaboration of a pre-construction meeting – and the problems it can thwart – cannot be measured in man-hours, materials, or dollars – it can be invaluable for the long-term success of the building.
3) Installation Training: Saving Time, Resources and Trouble When it's "Go-Time"
Chances are that the pre-construction meeting identified issues that will need to be addressed before the installation of the vapor intrusion mitigation system. Some issues, like scheduling, are common construction project “to-do’s” that fall into the natural order of the project timeline.
On a deeper level, however, a pre-slab meeting might expose the fact that your installer:
- Doesn’t have the right means and methods to deliver a successful installation,
- Has not worked with a specific product before, or
- Is simply not up-to-speed on the latest standards required to deliver a properly installed system before concrete placement.
This is where collaboration with the manufacturer of the system becomes vital.
Does a manufacturer offer training in the installation of their products, accessories, and how to incorporate them into the entire system? This value-add is what sets manufacturers apart from their competitors; beware of any “solution” that does not come backed up with the support to train installers on the ways to deliver that solution. Some manufacturers may even certify certain contractors to progress toward the installation date with more assurance.
4) Plan Ahead to Verify Your Installation
This final step is not about a supernatural ability to “see the future.” The most efficient project design teams plan their success all the way down to the steps they know they’ll take after the vapor intrusion mitigation system is installed.
Two key steps can be put into place before the system is ever installed.
First, does the system’s manufacturer provide any service that reviews the installation? Perhaps this involves a manufacturer’s representative visiting the site to review the installation, or by verifying digitally representative images of the installation. Rewind to the vapor intrusion mitigation design plan mentioned in step #1 - this can be stipulated by an environmental engineer in their design plan! Thinking this far ahead will provide quality assurance on the back end that cannot be substituted after the fact.
Finally, what diagnostic tools will be used to verify the installation mitigates the intrusion of vapor? Most commonly, this involves a smoke test of the entire system to indicate if – and where – the system is not delivering the protection required. While this step happens after the installation, knowing that it must be done beforehand sets the right expectation for success.
Even the Best-Laid Plans Need... Planning
These four steps only begin to demonstrate the massive gap between the technical requirements that come in a written design plan for a vapor intrusion mitigation system and the practical demands that come by bringing stakeholders together to collaborate and identify issues before they arise.
How well a project team can bridge the gap between technical requirements and practical demands will often determine the overall success of the project.
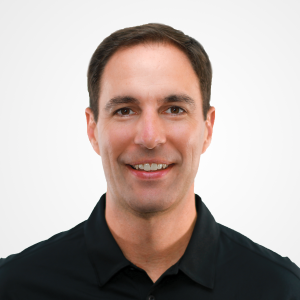
Written by Page Cotton
Page Cotton is the National Product Manager for Drago Wrap and Stego Wrap. Since 2005, he has had experience educating the industry about the effects of the below-slab environment on building health and its inhabitants. Page enjoys working as a trusted consultant to architects, engineers, and contractors to further their understanding of sub-slab barrier systems.
- Stego (26)
- StegoCrawl (24)
- Stego-Awareness (17)
- Case Studies (14)
- StegoHome (14)
- StegoCrawl-Consideration (12)
- StegoCrawl-Awareness (11)
- Customer Stories (9)
- Stego-Consideration (9)
- Pango (8)
- Beast (7)
- StegoHome-Awareness (7)
- StegoHome-Consideration (7)
- How to Install (6)
- Drago (5)
- Pango-Awareness (5)
- Beast-Awareness (4)
- Beast-Consideration (3)
- Drago-Awareness (3)
- Pango-Consideration (3)
- Stego IQ (3)
- Drago-Consideration (2)
- StegoCrawl-Decision (2)
Popular Posts
Stay Connected.
Enter your email below.
Post Comments