What Lies Beneath the Concrete Slab
3 Things to Consider When Preparing Your Subbase for an Under-Slab Vapor Barrier
Your concrete slab foundation, and what lies beneath it, is your foundation to success. When preparing the substructure of your concrete slab, there is prep work you can do to ensure long-term success.
What is an acceptable subbase for an under-slab vapor retarder?
This is one of the most common questions I get from our industry. The question is a good one; the subbase and subgrade structures can affect the performance of a slab-on-ground—and the building above—in multiple ways.
The array of knock-on effects a subbase material can have [on your project] always reminds me to add the caveat that you should always consult a qualified design professional when considering these factors. But we love a good question, and while it is generally the role of the geotechnical engineer to design the soil support system, we have asked several design and construction professionals to offer their insights and summarized those here.
The purpose of this article is to better understand the considerations that come into play when selecting, designing, or specifying a subbase directly below an under-slab vapor retarder.
LEARN MORE: What Makes a Vapor Barrier Different than a Vapor Retarder?
We find that, although design considerations may differ from site to site, there are several common elements to providing an acceptable subbase over which to install a vapor retarder. We hope these insights add to the decades of back-and-forth we have had with our always-inquisitive stakeholders.
Consideration #1: Stable and Uniform Slab Support
A properly graded and compacted subbase resists displacement.
Sound foundations begin by confirming that the soil structure and slab thickness meet the load bearing requirements of the building above. When it comes to heavily-loaded slabs-on-ground, long-term potential settlement is a key consideration. Similarly, if there is potential for instability of the subbase, it may be time to call in the concrete boom pump to avoid the heavy construction traffic of repetitive heavy mixing trucks rolling across the site.
Beyond structural considerations, project teams generally agree that the primary purpose of a subbase material is to provide a stable, uniform platform upon which to place the slab.
This can at times be accomplished by properly preparing (grading, compacting and treating, if necessary) existing native soils. A subbase of non-native fill, however, is often a critical addition for two reasons:
- It can make up for elevation lost due to compaction
- It can better resist rutting or displacement caused by wheeled construction traffic
Effective subbases are almost always comprised of trimmable fill, properly compacted and capable of supporting construction traffic without displacement. As you can see in the photo below, an uneven or poorly compacted subbase can lead to variations in slab thickness, which can then induce random cracking between contraction joints.
Uneven slab thickness can induce random cracking. PC: North S.Tarr Concrete Consulting, P.C.
The fill itself will need to incorporate properly sized and shaped stone, appropriately graded. Many combinations of stone can fill this role, and each geographic region likely will have its own common material specifications from which to select the right blend.
If poorly draining or lacking stability, a portion of the subgrade (native soil below the subbase) may also need to be removed and replaced with a well-graded fill. DOT-type road base often serves this purpose.
Consideration #2: Capillary Action – Below and Within the Concrete Slab
A low-permeance vapor barrier can help prevent liquid water from contacting the underside of the concrete slab.
Since 1998, we have warned of the impeding under-slab water vapor and its effects on the concrete slab. But it should never be forgotten that liquid water can pose equally pressing concerns for the success of a slab and the floorings or coatings that reside on top. The primary way liquid water can threaten a concrete slab: capillary action.
When it comes to slab-on-ground construction, capillary action is the ability of liquid water to rise to heights well above the measured water table when the soil structure above the water table is comprised of material with a sufficiently fine soil structure. In very fine soil structures, it is the cohesive nature of the water molecules and their adhesion to the soil particles that can lead to the vertical rise of liquid water to a height many feet above the water table.
If the potential for capillary rise is known and not properly addressed, it can spell disaster for floor covering or coating installations when liquid water reaches and contacts the underside of the slab.
So how do we address this risk? A low-permeance vapor barrier, properly installed directly below the slab may help to prevent liquid water from contacting the underside of the slab, but it is not intended to act as a waterproofing system, and it may not act as a sufficient capillary break.
Learn More: When and Where to Install a Below-Slab Vapor Barrier
The best option to prevent the capillary rise of liquid water below a concrete slab-on-ground is always to cut out a measure of the fine base material—most likely native soil--and replace it with a coarse material.
Free-draining, crushed or coarse fill materials widen the interstitial space (the gap) between the soil particles so capillary rise cannot occur.
What type of capillary break material to use and how much of the existing base material should be removed (if any), is up to the geotechnical firm involved during the design stage of the project.
When using a crushed stone material, if deemed necessary, the very top surface of the stone can be smoothed out with a fine grade material such as #10 sand, stone dust, or crusher fines. A very thin layer of the fine grade material smooths out the surface without choking off the open subbase or subgrade structure below that forms the capillary break.
Consideration #3: The Under-Slab Vapor Barrier Itself
The below-slab vapor barrier should be able to handle all sorts of construction traffic.
The first two considerations mentioned above are the most critical in subbase design. This is not to say that vapor barriers play no role when considering a subbase; but with today’s high-performance vapor barriers and standard subbase preparation practices, most of the work is done by default.
LEARN MORE: 10 Critical Reasons Why You Need a Below-Slab Vapor Barrier
ASTM E1643-18a, the standard practice for under-slab vapor retarder installation, comes closest to providing a recommendation that ties the subbase material to the vapor retarder. In section 5.3.5, the standard mentions that selection of the vapor retarder should be in part determined by the subbase, specifically encouraging the project team to “select [a] vapor retarder material capable of withstanding tear or puncture damage due to the type, gradation, and texture of the base material to be installed below the material. Prepare base material to minimize risk of puncture, for example, by rolling or compacting.”
LEARN MORE: What is ASTM E1643? Summing Up Vapor Barrier Installation Standards
Leveling, rolling and compacting a properly graded subbase material will all but eliminate the upturned protrusion of angular stone particles that can lead to puncture of many types of generic vapor retarder materials when heavy traffic wheels across. Whenever traffic from ready-mix trucks, laser screeds, concrete pumps, or concrete buggies will take place directly over the vapor retarder, it is always best to specify and install a high-performance vapor retarder that meets the Class A requirements of ASTM E1745-17.
LEARN MORE: What is ASTM E1745? Understanding the Standard and its Classifications
Class A materials are engineered to best resist punctures and tears, greatly reducing the potential for damage to the vapor retarder. The rare puncture is easy to repair.
The Answer?
So what lies beneath the concrete slab? As always, every project is different. But knowing the list of considerations – and their underlying importance – can help in designing the substructure of your next project.
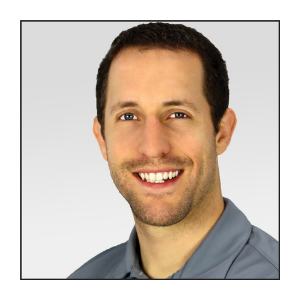
Written by Dan Marks
Dan Marks was the former Technical Director at Stego Industries, LLC.
- Stego (25)
- StegoCrawl (24)
- Stego-Awareness (17)
- Case Studies (14)
- StegoHome (14)
- StegoCrawl-Consideration (12)
- StegoCrawl-Awareness (11)
- Customer Stories (9)
- Pango (8)
- Stego-Consideration (8)
- Beast (7)
- StegoHome-Awareness (7)
- StegoHome-Consideration (7)
- How to Install (6)
- Drago (5)
- Pango-Awareness (5)
- Beast-Awareness (4)
- Beast-Consideration (3)
- Drago-Awareness (3)
- Pango-Consideration (3)
- Stego IQ (3)
- Drago-Consideration (2)
- StegoCrawl-Decision (2)
Popular Posts
Stay Connected.
Enter your email below.
Post Comments