A 10-Point Checklist for Common Crawl Space Building Codes
It would be a mistake to spend the time, money, and effort to rehabilitate your crawl space, only to find out afterwards that the work you did isn’t even up to code. Code is complicated for many reasons including but not limited to: finding which codes are applicable to your project and interpreting code the same way as your local inspector. Determining local code is difficult because there is the overarching International Residential Code (IRC) that acts as a baseline for proper building code requirements, but there are also local building codes that may differ from the national requirements.
Download Now: Crawl Space Building Code Checklist
Interpreting code is not always straightforward either. I was in a meeting not long ago with code officials representing different jurisdictions in my home state and as we were discussing one particular sentence of code, it became clear that all three officials had a different interpretation of the same sentence. Talk about an uphill battle!
So, in this post we’ve at least centralized the code requirements, and we’ve also provided a few additional best practices we thought might make your project research a little easier. Of course, we have to disclaim that it is always prudent to check with your local regulatory department before proceeding with your project, just to make sure you are in compliance with all the unique code requirements of your area. Without further ado:
1. Seal or remove crawl space vents
Some people assume that foundation wall vents can help prevent moisture and rot in a crawl space, but building codes do not require them when properly encapsulating a crawl space with a Class I vapor retarder and conditioned air supply is in place (Source: 2015 IRC – Section R408.3).
2. Access door to the crawl space must conform to specifications
In order to ensure ease of access to the crawl space, any access door must be at least 18x24 inches (Source: 2015 International Residential Code (IRC) - Section R408.4).
3. Vapor retarder must be used on ground
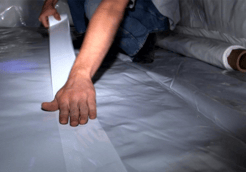
Crawl space encapsulation methods must include protection from ground water entry. Exposed earth in unvented crawl space foundations shall be covered with a continuous, minimum 6-mil polyethylene vapor retarder (2012 IRC Section R408.2) and it must be a Class I vapor retarder (IRC 2012 – N1102.1.10). Vapor barriers should be secured to the ground floor, covering any exposed dirt. Joints must overlap no less than 6 inches, and all seams must be taped (Source: 2015 IRC - Section 408.3.1).
4. Drain and vent terminations need to meet specifications
The surface of the crawl space floor must slope to a drain or sump pump. Any drain located in the crawl space must be allowed to run off and terminate outdoors or to an interior crawl space drain or sump pump. Crawl space drains may not run off to gutters or foundation perimeter drains, and dryer vents must be terminated outdoors. As a more general observation, any building grade should allow water to drain away from the foundation of the crawl space (Source: 2015 IRC – Sections R405 and P2719).
5. Damp proofing materials for outside walls may be necessary
If the outside grade is higher than the inside grade of the crawl space, the exterior walls of the crawl space need to contain a damp proofing material, e.g. semi-rigid materials like mastic asphalt or rigid materials like brick, stone, mortar, or cement concrete. Damp proof materials must also be added at the top of the footing of the finished grade (Source: 2015 IRC - Section R406).
6. Air in the crawl space must be handled properly
If installing a Class I vapor retarder on the ground and up the vertical wall a minimum of 6 inches, it is required that the crawl space has either continuously operated mechanical exhaust ventilation, or conditioned air supply. Acceptable methods of mechanical drying are permanent dehumidifiers, supply air from the HVAC, conditioned air from the living space above, or exhaust fans (Source: 2015 IRC – Section R408.3.2.2.2).
7. Insulation requirements must be met
Thermal insulation must be located on the walls in a conditioned crawl space if the floor and wall is encapsulated with a Class I vapor retarder (Source: 2015 IRC – Section R408.3.2.2.2). Foam insulation boards must include a thermal barrier, which protects it against ignition. Porous insulation materials should not have ground contact (Source: 2015 IRC – Section R402.2.11 and Appendix N1102.2.11).
Once you know the minimum building code requirements for your area, there may be choices you can make where exceeding those minimums provides considerable value for your project. Here are examples of additional recommendations that you will want to consider:
1. Caulks and sealants must conform to specifications
Caulking or sealants should be used at each space separating the crawl space from the outside. Special attention should be given to areas between sill plates, the foundation, and any openings at plumbing pipes, as well as penetrations at electrical, gas, and mechanical lines. Any caulks or sealants used should have the capability to block air flow effectively.
2. Termite inspection gap should be in place
In certain states, termites cause more of a threat than others. Before encapsulating your crawl space, you will want to double-check with your local building code regarding details on termite inspection gaps. Some states will require a clear, unobstructed three-inch minimum gap between the top of the wall liner and the bottom of the wood sill. This will enable termite inspections without the necessity of removing or disturbing the encapsulation envelope. Terminating the vapor barrier at the proper height may save you some major headaches down the road.
3. Pay attention to permeance
Even though the IRC requires a minimum 6-mil vapor retarder, the amount of moisture passing through generic 6-mil materials may be in excess of what is healthy for your home. Many crawl space contractors use heavier gauge materials for durability and permeance. Commonly made up of recycled plastics, 6-mil poly is a weak vapor retarder and one that allows too much moisture vapor to pass through the liner. By investing in a lower permeance vapor barrier at the start, you will minimize moisture problems in the future. Our recent blog post further discusses the inadequacy of 6-mil poly.
Mitigate your risk of mold, odors, and poor indoor air-quality by following these building codes and best practices listed from your friends at Stego Industries. Many local building departments are rapidly moving past these minimum code requirements and enforcing stricter regulations on materials used for crawl space enclosure. Because of this, it’s a good idea to choose products and materials that meet and exceed ASTM E1745 standards and that have a permeance below 0.01 perms before and after conditioning. Proper crawl space encapsulation is completed through the use of superior products.
Our goal at Stego® Industries is to ensure safe and healthy crawl spaces. If you are looking for materials to encapsulate your space, we can offer industry-leading products that exceed minimum code standards and many more resources to help you with your projects. Contact us for more information about our crawl space encapsulation products, including StegoCrawl® Wrap.
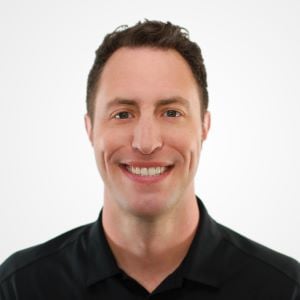
Written by Tom Marks
Tom Marks is the Business Development Project Manager with Stego Industries, LLC. He has been with Stego since 2007, serving many years as the Rocky Mountains Regional Manager. Now, his focus is geared toward vapor barrier solutions for new and existing homes as the Product Manager of the StegoHome and StegoCrawl brands. In addition, Tom serves as Sustainability Manager, overseeing Stego’s leadership in holistic product and corporate sustainability. Tom enjoys working with a wide range of project team members and customers to incorporate effective sub-slab vapor protection and create healthy, sustainable homes and buildings.
- Stego (26)
- StegoCrawl (24)
- Stego-Awareness (17)
- Case Studies (14)
- StegoHome (14)
- StegoCrawl-Consideration (12)
- StegoCrawl-Awareness (11)
- Customer Stories (9)
- Stego-Consideration (9)
- Pango (8)
- Beast (7)
- StegoHome-Awareness (7)
- StegoHome-Consideration (7)
- How to Install (6)
- Drago (5)
- Pango-Awareness (5)
- Beast-Awareness (4)
- Beast-Consideration (3)
- Drago-Awareness (3)
- Pango-Consideration (3)
- Stego IQ (3)
- Drago-Consideration (2)
- StegoCrawl-Decision (2)
Popular Posts
Stay Connected.
Enter your email below.
Post Comments