3 Critical Problems with Generic 6-Mil Poly Sheeting Below a Concrete Slab
Why Cheap, Commodity "Visqueen" May Cost You More In the Long Run
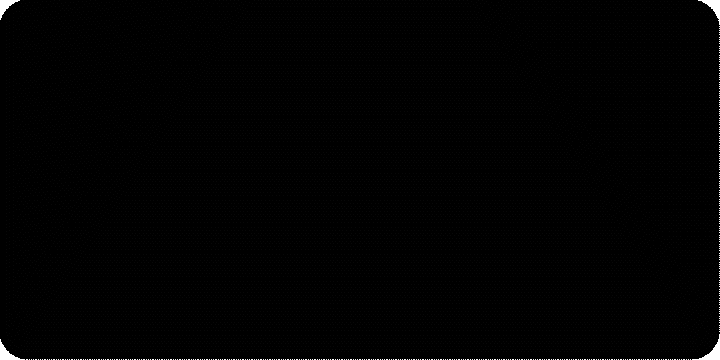
One of the most important characteristics of an effective under-slab vapor barrier is durability. If a material is damaged or deteriorates, it may fail to appropriately protect the concrete floor slab and building envelope above. Damage could happen moments after it is installed (if it is punctured or torn before concrete placement) or beneath the placed slab over time (because the material lacked the necessary performance characteristics to withstand the relatively harsh below-slab environment).
Don’t get us wrong, generic poly sheeting has a useful place for myriad applications and uses, including in the construction industry. In fact, it may appropriate as a “vapor retarder” in other areas of the building enclosure, such as allowable within code for use in above-grade walls in some climate zones. But, again, that is just a very different condition compared to beneath the slab, in terms of necessary water vapor permeance, strength, in-service exposures, etc.
In this article, I’ll review the 3 main problems with generic poly plastic sheeting when used in a below-slab application for new buildings and homes. You’ll see exactly why selecting engineered, high-performance vapor barriers matters to the entire spectrum of building project team members: owners, designers, contractors, homebuilders, and homeowners.
-
Problem #1: Low-Quality, Recycled Resins Make for Weak, Ineffective Plastic Sheeting
-
Problem #2: Lack of Antioxidants
-
Problem #3: Lacking Multi-Layer Co-Extrusion
Generic, low-quality polyethylene (often referred to as visqueen, although “Visqueen” is in fact a trade name of British Polythene Limited and sold as a quality brand in the UK) is perhaps the best example of a material now considered to be defective when installed beneath the slab. Visqueen is often unlikely to withstand either the rigors of the installation and concrete placement process or avoid degrees of degradation over time, which often go hand-in-hand.
Perhaps even more alarming, generic (often 6-mil thick) poly sheeting has been especially common in residential construction to satisfy historical bare minimum code requirements.
The easiest way to understand why generic poly is defective when installed beneath a slab is to hold it in one hand, while holding in the other a vapor barrier material that meets Class A of the standard specification for plastic water vapor retarders, ASTM E1745. Poly is thin, riddled with inconsistencies (e.g., nodules, variations in thickness), and relatively easy to tear, while a Class A vapor barrier is the opposite.
Since you may not be holding samples of material while reading this article, the next best thing is to gain an understanding of how high-performance plastic sheeting, specifically those designed as under-slab vapor barriers, are engineered.
Problem #1: Low-Quality, Recycled Resins Make for Weak, Ineffective Plastic Sheeting
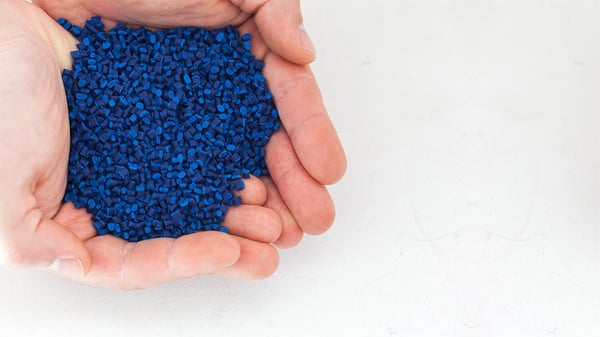
The first problem is a complex, material science matter, but even a basic knowledge of polymer chemistry makes it easy to understand. Here we go:
High-performance under-slab vapor barriers primarily utilize polyolefins. “Olefin” refers to class of plastic monomers (e.g. ethylene, propylene) with different atomic structures and “poly” denotes that these materials are strung together in large chains. The lengths of these chains and degree of branching along them in large part determine> the quality of the resins and many of the physical characteristics of finished goods utilizing them. Polymer branching correlates with the density of the bulk plastic; thus, especially when dealing with polyethylene, we tend to classify products by their density (e.g. low-density polyethylene [LDPE], high-density polyethylene [HDPE], etc.).
The “right” chains—with sufficient chain length and amount of branching, etc.— require a large degree of science and technology, but many of the firms making polymer resins are very skilled at what they do. These resin suppliers can produce an array of materials with varying degrees of conformance to almost any material specification an end-user can dream up (with costs often increasing alongside performance). To achieve the desired properties in an under-slab plastic sheeting as indicated below—prime resins are the key.
- Impact resistance: its ability to withstand punctures
- Tensile strength: its ability to withstand stretching or tearing
- Water vapor permeability: its ability to prevent water vapor diffusion through the membrane
“Prime” means resins meet specific material specifications; thus, using prime resins provides assurance that the right physical properties can be obtained when the pelletized prime resins are compounded, extruded, and blown into plastic sheeting. Aside from prime, resins may fall into other classes, with quality (or at least consistency) suffering as one moves down the hierarchy. Near the bottom is “wide spec” (often called “off-grade” or “off-spec”), the feedstock of most generic plastic sheeting (like those used to make trash bags).
Virgin resins are those that have yet to be made into a finished good. In contrast to virgin, recycled resins go through a re-melting process (which involves heat) that breaks down its chemical chains. Further, the more a material is recycled, the more that heat history can impact the final product, including concentrated pockets of crosslinked, non-melted materials, which are seen as gels (hard nodules) in the material. Both of these issues can lead to embedded defects and loss of key strength properties.
An under-slab vapor retarder with this problem -- inferior content/composition -- is unlikely to stand up to the demands of common installation conditions, construction traffic, and the process of placing concrete leading to subpar protection in the installed system. Additionally, the inconsistent performance of traditional 6-mil poly sheeting, often made from recycled resins, makes it difficult to help quantify its effectiveness for impeding radon diffusion.
Problem #2: Lack of Antioxidants: Oxidation and Its Unforgiving Effect on Plastic Sheeting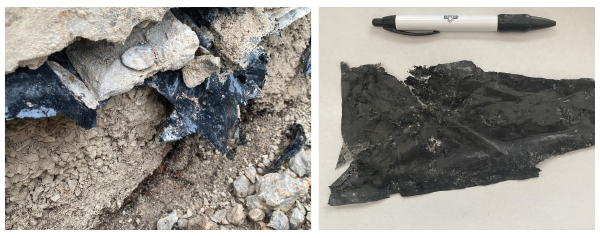
As mentioned, processing (and reprocessing) of plastic resins involves a great deal of heat energy. This added energy not only can break polymer chains, decreasing the length of chains that is a major factor in the strength of the plastic, but it can also increase oxidation along a chain, a process by which electrons are stripped from the polymer. This can lead to chain scission. Oxidation will attach to polymer chain, which will make the polymer more hydrophilic, causing the moisture permeance to increase, which can also adversely affect the properties of the finished good.
In this way, reprocessed or recycled material is often weaker than the original plastic that provided the raw material and may lack the other desired properties. If this recycling contributes to the reuse of a trash bag or a park bench, we can all see the value of reprocessing and reuse. But when the material is meant to protect a built environment for the life of the building, a recycled or reprocessed material is rarely – if ever – up to the task.
Oxidation, as described above, is an unforgiving process that affects many plastics negatively. The concerns intensify in an under-slab application due to the oxidation that can occur at different stages these membranes are used: due to sunlight (UV) after installation and before slab placement and beneath the slab over time. Even more, the degree of oxidation increases the more it is recycled, making the impact on low-quality poly greater than the impact on virgin material.
In some ways, there are 3 variables in the function of visqueen’s defectiveness; it not only:
- fails to withstand installation and;
- degrades over time, but chances are that;
- oxidation has already gone to work on the material before it ever rolls out on the jobsite.
Problem #3: Lacking Multi-Layer Co-Extrusion: Recycled Plastic Is Only As Good As Its Weakest Link
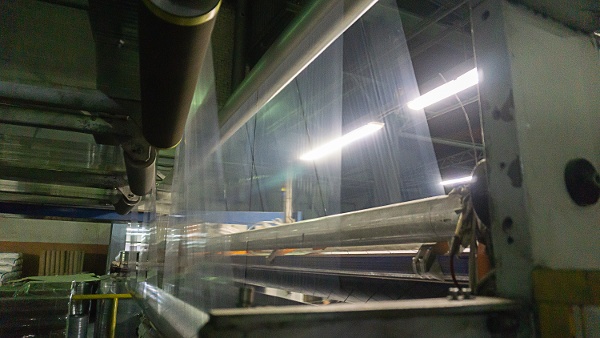
Not all of the properties necessary for an effective under-slab vapor barrier (puncture strength, permeance, chemical resistance, etc.) are gained by a single polymer/density combination. The most effective high-performance under-slab vapor barriers are often “engineered”, essentially meaning multi-layered co-extrusions of different densities (or even different polymers or co-polymers) which isolate the function of each layer from its neighboring counterparts.
For example, materials that are best suited to resist degradation to chemicals found in the soil, or that best hold up to the wear and tear of jobsite traffic, can be located at the outer layers, protecting inner layers of a multi-layer, co-extruded plastic sheeting more effectively, allowing them to fulfill whatever specialized role they may take for the plastic sheeting (e.g. low permeability).
A generic poly plastic made of recycled resins is most often intended to be cheap. Thus, there is likely little specialization in the layers, if it is even co-extruded at all. It is very unlikely that one of these commodity plastic sheets would employ layers for a strategic purpose. You are far more likely to find average properties through and across the plastic. The result: individual properties of the whole plastic sheet, compared to a co-extrusion with specialized layers, tend to suffer – the end product is less than the sum of its parts.
How generic poly is made explains why it is cheap but is also a big reason for its defectiveness as an under-slab vapor retarder.
The Choice is Clear and Critical
Your building products need to stand the test of time and maintain their integrity throughout the building’s lifetime. Generic poly can fail in this regard beneath a slab, which can lead to a cascade of other problems over the life of the building or home – such as the integrity of the concrete foundation, the indoor air quality, and in the potential failure of other building components, like flooring.
Note: consider the use of high-performance, engineered vapor barriers as ground cover in crawl spaces in new construction as well. In many ways, the problems associated with generic poly sheeting outlined in this article beneath slabs can apply to their common use in crawl space encapsulation, including concerns with strength, long-term vapor protection, and even quality of the installation.
You only have one chance to place proper vapor protection below your building or home, so why take a chance with building products that are not engineered for long-term protection?
Editor's note: This blog post was initially published in November 2020 and has been revised to stay up-to-date.
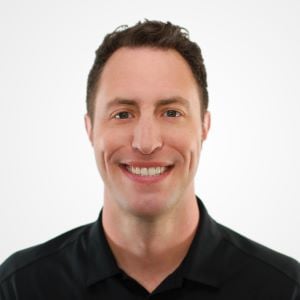
Written by Tom Marks
Tom Marks is the Business Development Project Manager with Stego Industries, LLC. He has been with Stego since 2007, serving many years as the Rocky Mountains Regional Manager. Now, his focus is geared toward vapor barrier solutions for new and existing homes as the Product Manager of the StegoHome and StegoCrawl brands. In addition, Tom serves as Sustainability Manager, overseeing Stego’s leadership in holistic product and corporate sustainability. Tom enjoys working with a wide range of project team members and customers to incorporate effective sub-slab vapor protection and create healthy, sustainable homes and buildings.
- Stego (26)
- StegoCrawl (24)
- Stego-Awareness (17)
- Case Studies (14)
- StegoHome (14)
- StegoCrawl-Consideration (12)
- StegoCrawl-Awareness (11)
- Customer Stories (9)
- Stego-Consideration (9)
- Pango (8)
- Beast (7)
- StegoHome-Awareness (7)
- StegoHome-Consideration (7)
- How to Install (6)
- Drago (5)
- Pango-Awareness (5)
- Beast-Awareness (4)
- Beast-Consideration (3)
- Drago-Awareness (3)
- Pango-Consideration (3)
- Stego IQ (3)
- Drago-Consideration (2)
- StegoCrawl-Decision (2)
Popular Posts
Stay Connected.
Enter your email below.
Post Comments