Where to Place Under-Slab Insulation? Above or Below the Vapor Barrier
What the Experts Have to Say about Where Insulation Should Be Placed in Relative Position to the Vapor Barrier
You definitely should do this. You also definitely should not do this. People who do this don’t know what they’re talking about. That said, people who do not do this are fools!
There, I think we just carefully summed up most conversations about building practices. Worse, this is a pretty good recap of most online discussions about any topic these days.
Clicking the ‘reply’ or ‘comment’ button can be so instantly satisfying. We’ve all been guilty of this at some point.
What all these instantly gratifying online spats are missing is perspective. In the building practices conversation, those perspectives might sound like this: where are you building? On what are you building? What are you trying to achieve? What will the building be used for? What does your building code say? Have you asked your design professional? How much do you want to spend?
Here’s a perfect topic to demonstrate this, something I get asked about a lot: insulation beneath concrete.
The use of insulation below a slab in a residential or commercial new build is not universal and is highly driven by local climates.
In some areas of the country, a casual observer could be forgiven for thinking no one ever made an attempt to thermally isolate the foundation from the exterior environment (that’s the “you should never do this” crowd in our example). In other areas of the country, this is second nature (“you should always do this!” according to our example).
So let me offer some perspective: because the application of under-slab insulation is geographically varied, knowing how to sequence it with the under-slab vapor barrier is a common point of uncertainty in the minds of building owners, homebuilders, contractors, and even design professionals.
Some more perspective: I won’t aim to provide a definitive answer regarding how these components should be installed relative to one another for all permutations of climate, foundation construction, building application, type of insulation, etc. I’m not here to be just another person polluting the building practices conversation with “certainties” that lack perspective. My goals are to relay some of the prevailing basic wisdom currently published on this topic and to communicate Stego’s general insight and recommendations on this unclear question.
Where Should Insulation Be Placed?
The question at hand often boils down to this: Should the vapor barrier be placed below the insulation, or should the insulation be installed first so that the vapor barrier is directly below the cast concrete slab?
We (Stego) do not have a specific recommendation regarding this sequence. However, we can say that a properly installed under-slab vapor barrier, like Stego Wrap or StegoHome, can perform its intended function—to impede the permeation of under-slab water vapor from the ground—if located in either configuration.
For not forcing anyone’s hand in this decision, telling them to do something they perhaps do not want to do, you are welcome. But, given we always aim to provide a little better guidance than “sorry, ask your design professional,” please read on.
Under-Slab Insulation Below the Vapor Barrier 🡻
On most projects where insulation meets the under-slab vapor barrier, we have found that the project teams elect to install their insulation first and to lay the vapor barrier over top. Various industry leaders have commented on the advantage of placing the vapor barrier directly beneath the slab. Joe Lstiburek, the founding principal with Building Science Corporation and who authored a very useful article on slab insulation, captions a photo of an advantageous residential slab design with these words:
Notice that the... vapor barrier is located on top of the rigid insulation between the rigid insulation and the bottom surface of the concrete—in direct contact with the concrete. Do not, and I repeat, do not locate the [vapor barrier] under the insulation as it will keep the insulation wet. Trust me on this...
Others have made the same point for similar reasons. For example, placing the vapor barrier directly beneath the concrete reduces the chance of mix/bleed water infiltrating the insulation where it may:
- adversely affect the R-value of the insulation, reducing its efficacy, and/or
- subsequently diffuse back through the slab, potentially contributing to flooring failures and/or other moisture-related issues.
We have also heard the argument for this approach coming from the standpoint that the vapor barrier plays a role in preventing “iceberg-ing” of the insulation. This occurs when rigid foam insulation isn't sealed well at the joints, causing it to get lifted and displaced as wet, newly placed concrete flows between the joints and beneath the panels.
Under-Slab Insulation Above the Vapor Barrier 🡹
Conversely, it has been argued in some cases that a better method of keeping the insulation dry is in fact to isolate the insulation from the sub-grade by means of the vapor barrier being installed first. Part of this reasoning may relate to the fact that any soil is inherently “wet” to some degree (or can become so) and can therefore adversely affect the insulation’s insulative properties. Similarly, under-slab water vapor can accumulate beneath a nearly impermeable, under-slab material like a vapor barrier and further increase the localized amount of moisture surrounding/contacting any insulation installed below said barrier. Where the slab is expected to be cool in relation to the ground, this becomes a greater concern; it also implies that perhaps this is less a concern for residential slab-on-ground new builds than for certain commercial, cold-storage applications.
Another instance we often see project teams elect to locate the under-slab vapor barrier beneath the insulation is when some sort of in-floor heating is used in the concrete slab (e.g., radiant or hydronic). In this case, the insulation placed in this orientation may help provide a “buffer” between the heat components and the vapor barrier, as well as may help eliminate the potential for penetrations of the vapor barrier given how some in-floor heat systems are installed.
Consult the Design Professional
Given that various factors can dictate the sequence of these important materials, the location of the vapor barrier and insulation in relative position to one another should be evaluated by each project’s design professional of record. This isn’t a cop-out; their perspective in these decisions is why you hired them. They also tend to be the best trained arbiters of these other perspectives (geography, objectives, codes, and best practices) because of their experience!
The manufacturer of the insulation product(s) may also have special considerations that will affect the order/configuration of their systems. Once that sequence has been selected, Stego simply recommends that Stego barrier solutions be installed according to our installation instructions, per ASTM E1643.
One Last Question: Is a Vapor Barrier Even Needed When Under-Slab Insulation is Used?
Yes, we think so. Maybe not surprising in a blog from an under-slab vapor barrier company but let us explain by briefly digging into some specifics.
We’ve noticed some sentiment from the industry (especially in the residential landscape) that some types of under-slab insulation offer effective water vapor protection to allow for omission of a typical plastic sheet vapor barrier beneath the slab. While some types of under-slab insulation may have a decent water vapor permeance – at least to be considered a “vapor retarder” in an above-grade wall section of the building code – there is more to it when we talk about under-slab water vapor protection.
Often at typical thicknesses, under-slab insulation will offer a water vapor permeance to only meet a Class II or greater (higher permeance) vapor retarder classification in the code (2021 IRC Section R702.7)12. This is where the definitions matter…although called a “vapor retarder”, Class II materials (with a water vapor permeance between 0.1 to 1.0 perms) simply aren’t appropriate to protect the underside of the home or building. You can read more about confusion surrounding “vapor retarders” and “vapor barriers” across the building enclosure in our blog series on the subject.
Even if some insulation has a lower water vapor permeance (say less than 0.1 perms or Class I), published industry guidance and best practices offer even more prescriptive criteria for what makes effective vapor control beneath concrete floor slabs. Namely, the 2021 IRC (and guidance from the American Concrete Institute, EPA, and more) reference vapor retarders beneath concrete floor slabs should meet a robust performance standard, ASTM E1745. This standard includes testing to ensure materials used in this application are well suited for durability during installation and maintain an effective water vapor permeance for a long period of time beneath the slab. It is also worth noting that ASTM E1745 applies specifically to “flexible, preformed sheet membrane materials”.
Thus, in our estimation, under-slab insulation should be evaluated and selected largely based on its properties and utility as insulation and not as the primary component for appropriately controlling water vapor diffusion.
Of course, none of this should be construed as a criticism of insulation. Insulation is critical to the:
- comfort,
- energy efficiency, and
- overall performance of a home or building.
It also plays a role in helping prevent moisture-related issues caused by water vapor diffusion via raising the dew point temperature of surfaces. In fact, it may have many useful benefits in an under-slab application not addressed here – closed-cell spray foam is a very good air barrier, for example. As far as we’re concerned, use as much under-slab insulation as you can to meet performance and budget (and code) needs. We just want builders to be careful not to omit an effective ASTM E1745-compliant vapor barrier without this more comprehensive understanding. I can’t wait to read the comments on this article. Here’s to hoping the perspectives shared don’t prove my point involving conversations about building practices.
Editor's note: This blog post was initially written in February 2023 and has been revised to stay up-to-date.
[1] Water vapor permeance of XPS rigid foam insulation approx. 1.1 perms at 1’’: https://www.constructionspecifier.com/comparing-polystyrenes-looking-at-the-differences-between-eps-and-xps/2/
[2] Water vapor permeance of closed-cell spray foam insulation approx. 1 perm at 2’’ thick: https://www1.eere.energy.gov/buildings/publications/pdfs/building_america/spray_foam_guide.pdf
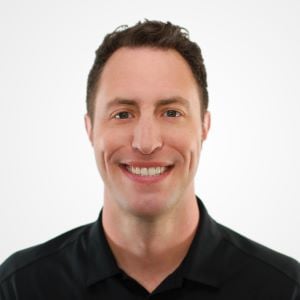
Written by Tom Marks
Tom Marks is the Business Development Project Manager with Stego Industries, LLC. He has been with Stego since 2007, serving many years as the Rocky Mountains Regional Manager. Now, his focus is geared toward vapor barrier solutions for new and existing homes as the Product Manager of the StegoHome and StegoCrawl brands. In addition, Tom serves as Sustainability Manager, overseeing Stego’s leadership in holistic product and corporate sustainability. Tom enjoys working with a wide range of project team members and customers to incorporate effective sub-slab vapor protection and create healthy, sustainable homes and buildings.
- Stego (26)
- StegoCrawl (24)
- Stego-Awareness (17)
- Case Studies (14)
- StegoHome (14)
- StegoCrawl-Consideration (12)
- StegoCrawl-Awareness (11)
- Customer Stories (9)
- Stego-Consideration (9)
- Pango (8)
- Beast (7)
- StegoHome-Awareness (7)
- StegoHome-Consideration (7)
- How to Install (6)
- Drago (5)
- Pango-Awareness (5)
- Beast-Awareness (4)
- Beast-Consideration (3)
- Drago-Awareness (3)
- Pango-Consideration (3)
- Stego IQ (3)
- Drago-Consideration (2)
- StegoCrawl-Decision (2)
Popular Posts
Stay Connected.
Enter your email below.
Post Comments