Termite and Moisture Barrier Terms You Should Know + Free Guide
Understanding These Terms Will Help Ensure Your Under-Slab or Crawl Space Vapor Barrier Installation is a Success
.png?width=720&name=TERMITE%20%26%20MOISTURE%20BARRIER%20TERMS%20(9).png)
When considering under slab or crawl space vapor protection for your project, it is important to consider your termite protection as well. After all, the foundation is an important part of your structure, and you want to do everything you can the first go around to protect it. The types of materials you select impact how to prepare your site correctly and sequence its construction efficiently.
This topic is also a great opportunity to sort through some commonly used terms and why they are relevant to your construction and product selection.
To properly install a physical termite vapor barrier prior to slab placement or within your existing crawl space, always review the installation instructions for the product you intend to use. If installing Pango Wrap® Termite/Vapor Barrier, you can review the installation instructions here.
But without an understanding of commonly used terms, any set of installation instructions can be daunting. It might be a good idea to review the compiled list of common under-slab vapor barrier and physical termite barrier terms that are provided below.
Disclaimer: the scope of this guide and terms are for general reference only, specifically for vapor and moisture control at foundations – the first side of the building or home. The focus is on concrete slabs and crawl spaces that are on-grade, near, partly, or fully below grade. This is NOT intended to include envelope components outside the foundation, including air barriers, weather barriers, vapor retarders, or vapor barriers in above-grade walls or roofs, which have, in many cases, entirely different definitions and utility depending on climate and project conditions.
Moisture Barrier Specific Terminology
Water Vapor: The invisible, gaseous state of liquid water. To prevent water vapor from passing into your home, specific vapor-proofing products and practices will need to be implemented. Waterproofing methods and their associated products may not be sufficient.
Diffusion: The collective movement of any vapor, such as water vapor, from higher to lower concentrations. Diffusion is a primary mechanism by which water vapor can move through building materials and into a home’s envelope, even through concrete.
Permeance: The value of how much moisture can pass from one side of a membrane to the other. Typically, this amount is reported in perms and can be derived in this construction context via ASTM F1249 or ASTM E96. The lower the water vapor permeance of a membrane, the better it is at impeding the diffusion of water vapor.
Vapor Barrier: A foundation vapor control material, usually a membrane, with a water vapor permeance level of 0.01 perms or less after conditioning tests (sources: PCA and ACI). Vapor Barrier permeance of less than 0.01 perms can be achieved through the use of various materials, but in crawl spaces or below the concrete slab, it is typically only done so with a high-performance plastic sheet or aluminum liner. Buyer beware: “vapor barrier” is probably the most commonly misused term in the waterproofing industry – the term “vapor barrier” should not be used as marketing fluff – it has an actual definition. “Barrier” in the context of foundation construction does not mean that zero moisture passes from one side of the membrane to the other, but at an industry-established threshold. Please see “vapor proof” below for more explanation.
Vapor Retarder: Any below-slab or crawl space material, regardless of its composition, with a permeance greater than 0.01 perms), but less than 0.10 perms (Source: ASTM E1745). By way of comparison to a “vapor barrier”, a vapor retarder allows more moisture vapor to pass from one side of the membrane to the other.
Vapor Proof: Vapor Proof is a marketing term, but one that is typically used to convey impermeability to a problematic volume of water vapor. In reality, practically nothing is impervious to the penetration of vapor. Even a block of steel has a permeance value, it’s just a matter of how many zeros occur after the decimal point prior to the eventual 1. If you want to understand how much moisture vapor passes from one side of any membrane to the other, find the product’s ASTM F1249 or ASTM E96 permeance value. Your goal is to keep your crawl space or concrete slab as protected from vapor sources as is reasonable and cost-effective. Proper installation of the materials you choose will be vital to achieving that goal.
Tensile Strength: A value that demonstrates how much tension is acceptable until failure is achieved. Failure, in the case of tensile strength, is a fracture or tear. The corresponding value indicates how much pressure can be applied until a material tears. Ideally, the material you select for your crawl space or below-slab vapor barrier will be able to withstand a great deal of pressure before tearing, because tears would render the material’s low permeance irrelevant. In this construction context, tensile strength values will be reported from ASTM D882.
Puncture Resistance: An indication of the strength of a product, measuring its ability to resist forces that might induce holes or other intrusion by a foreign object. Most commonly, puncture resistance testing is conducted with either a “falling dart” impact test (ASTM D1709) or by measuring the pressure applied from a metal rod/plunger in a “push-through test (ASTM D4833). Ideally, a product will be able to resist both dynamic impacts (falling dart) and consistently applied pressures (push-through), depending on the application in which it is used. As is the case with tensile strength, puncture resistance is important to maintaining the integrity of both the vapor and termite barrier protection – any puncture can make its permeance irrelevant.
Termite Barrier Specific Terminology
Physical Barrier (aka Barrier Product): Taken directly from the EPA website, there are 3 criteria that must be met for a product to be considered a physical barrier:
- The product is not intended to prevent, destroy, repel, or mitigate a pest, or to defoliate, desiccate or regulate the growth of plants.
- The product or article does not make a pesticidal claim on the labeling or in connection with sale and distribution.
- The product is intended to exclude pests only by providing a physical barrier against pest access and contains no toxicants (i.e., certain pruning paints for trees).
For the consumer, the important aspect of a physical barrier is that it does not contain any pesticides or toxicants. A physical barrier simply acts as an impenetrable layer of protection.
Integrated Pest Management (IPM): IPM is a pest management strategy that aims to reduce -- if not eliminate -- the use of pesticides. An IPM strategy approaches pest management from multiple angles (i.e., habitat manipulation, landscaping decisions, building design, and physical barriers). This strategy is a “green,” environmentally friendly approach that does not rely on unnecessary applications of pesticides. Pesticides do have their place within IPM, but never in pretreatment application. Pesticides may be applied if evidence of attack is identified and only targeted toward the species present.
Subterranean Termite: There are many species of subterranean termites throughout the U.S. and world. The designation of “subterranean” means that these species live, travel, and emerge from underground. Protecting your structure with an under-slab physical termite barrier is an excellent strategy to keep these invaders in the soil and out of your home. Expansion joints, conduits, plumbing penetrations, and cracks in concrete are all very common points of attack for subterranean termites.
Drywood Termite: Drywood termite species are the above-ground counterparts to subterranean termites. As their name implies, they primarily feed on dry wood above ground. While an under-slab physical barrier is a great idea for protection from subterranean termites, they do not address situations where drywood/above-ground termites are a concern.
Mud Tubes: Subterranean termites often seek food and sometimes shelter above the soil. To reach these areas, subterranean termites will build tunnels of mud to protect themselves from desiccation and predation. These mud tubes can often be found on foundation walls, providing a travel corridor between the safety of moist soil and their food source: your home.
Formosan Termite (Coptotermes Formosanus): Formosan termites are widely considered to be the most aggressive and destructive subterranean termite species in the U.S. They are an invasive species originally from Southeast Asia that have become ubiquitous throughout the Southern U.S. and Hawaii. They are noted for their massive colony sizes, extended foraging range (300 feet or more), and the speed with which a colony can cause significant and expensive structural damage.
Eastern Subterranean Termite (Reticulitermes Flavipes): Eastern “subs” are the most common native subterranean termite in the U.S. They can be found in every state except Alaska, but are more commonly found in the warmer southern half of the U.S. While they may not have the colony size of their Formosan cousins, they are no less voracious in their appetite for cellulose. Formosan termites get all the alarmist headlines, but the eastern subterranean termite is most common in the U.S.
Crawl Space Specific Terminology
Waterproofing: The act of making something impervious to liquid water. This can come in the form of positive waterproofing solutions at the outside or negative waterproofing solutions at the inside of a structure. Effective waterproofing at the foundation is critical given its connection to the soil and sources of liquid water.
Waterproof: Impervious to the penetration of liquid water. Note – this does not mean impervious to the diffusive movement of water vapor. A system designed to waterproof at the foundation of a home or building may not necessarily be vapor proof.
Negative Side: Moisture control from the inside of a home (meaning moisture has already passed through the structure wall before it’s controlled). This could be much less expensive than positive side moisture control for an existing home presenting leaks after its construction. Vapor barriers installed in the crawlspace or on the vertical wall of a basement are an example of negative side moisture protection.
Positive Side: Moisture protection from the outside of a home (meaning you deter moisture before it ever enters a structure). An example of positive side moisture control is waterproofing membranes applied to the exterior of a structure while it is under construction. It is more cost-effective to install positive side protection during construction rather than after the building has been constructed.
Rigid Foam Board Insulation: A foam-based insulation material that comes in a pre-fabricated rigid board. Rigid foam board insulation comes in a variety of options, including expanded polystyrene (EPS), extruded polystyrene (XPS), and polyiso (polyisocyanurate). Its closed-cell structure provides a great R-Value, good air sealing properties, and density to help resist water absorption. It is lightweight and easy to cut to size, making it a common option in crawl spaces and other below-grade applications. Keep in mind, closed-cell composition and low moisture absorption does not generally translate to a low water vapor permeance with unfaced rigid foam board insulation. This insulation alone, particularly with unsealed seams, would not be adequate as a vapor retarder/barrier in a foundation application.
Batt Insulation: This is the fiberglass (or mineral wool) insulation material you can buy from your hardware store that often may look like pink cotton candy. It is an open-cell insulation, providing decent R-Value but is not good for air sealing or vapor control. Because of its porous composition, you will want to avoid using this material in areas with moisture present. It can wick moisture and will lose its effectiveness once wet.
Spray Polyurethane Foam (SPF): SPF can come in two categories: closed cell and open cell. For crawl space applications, closed-cell SPF is typically used, due to its ability to block (not absorb) liquid moisture. SPF not only provides a good R-Value but is often used due to its air sealing characteristics. Homeowner beware: Inspection for termites is not possible behind or within SPF applications. If subterranean termites are a concern in your area, it is critical to terminate the SPF below the sill plate to allow for a termite inspection gap.
Termite Inspection Gap: Local building codes will require anywhere from two to six inches of bare foundation wall immediately below the sill plate (check your local codes for your area). Any insulation on the foundation wall must be terminated below the specified distance of this gap. The purpose of a termite inspection gap is to allow homeowners or pest management professionals the opportunity to inspect this area for evidence of termite activity.
Animal Exclusion: Rodents, bats, spiders, opossums, subterranean termites, and numerous other animals commonly seek food and shelter within crawl spaces. Vents, permanent penetrations, cracks in the concrete and the soil, are all common entry points for these pests. Exclusion involves sealing up these points of ingress with screens, sealants, and, in the case of termites, a physical termite barrier.
Thermal Load: Load on a structure created by changes in temperature, measured in watts. The thermal load is the amount of energy (heat) that needs to be added or removed from a house to maintain a regular temperature and control moisture, a job usually performed by a house’s HVAC system. Sources that affect thermal load are the outside air temperature, indoor air temperature, underground temperature, solar radiation, and heating and cooling (HVAC) equipment.
Closed Crawl Space: A closed crawl space is one encapsulated with a liner and all air gaps to the outside are sealed, preventing exterior moisture from entering the crawl space.
Open/Vented Crawl Space: A crawl space with open vents in the perimeter walls that allow air and moisture to pass from the exterior of the home to beneath the home. Recent studies demonstrate this leads to poorer indoor air quality (due to the higher likelihood of mold growth) and reduced energy efficiency.
Encapsulated Crawl Space: A crawl space completely sealed off to external air and moisture sources via a vapor barrier on the ground and vertical walls, sealing voids in the rim joist, and properly placed insulation at the perimeter walls. Also, see “closed crawl space”.
Conditioned Crawl Space: An encapsulated crawl space that incorporates controlled, mechanical air, such as integrated with the HVAC system, to maintain a dry and comfortable space similar to the rest of the home.
Stack/Chimney Effect: The natural movement of air in a home from low levels (basement/crawl space) to upper levels (2nd story). Natural convection draws air from down in your crawl space up into your living areas. If the air in your crawl space is moisture-laden or otherwise contaminated, this can cause reduced air quality, musty odors, and allows gases such as radon to infect your living space. A vapor barrier/retarder can prevent moist air and contribute to preventing other unwanted gases from entering your living space.
Spalling: The fractures that appear in the surface of your concrete due to the stress of repeated freezing and thawing cycles. Typically found in exterior concrete like a driveway, it may also be found on an exterior basement wall. If concrete spalling becomes significant, causing larger chunks of aggregate to break away from the wall, moisture could have access points to the interior of the home.
Aggregate: Coarse particulate material used in concrete, including gravel, sand, crushed stone, and slag.
Epoxy Injection: Method to fill in cracks in concrete walls to keep liquid water (not water vapor) from entering the foundation.
French Drain: Trench filled with a perforated corrugated pipe and gravel or rock to redirect surface water. French drains can be installed on the interior or the exterior around the perimeter of a structure to carry the water away. In crawl spaces, French drains either lead to the exterior of the home or to a pit and sump pump within the crawl space in order to mechanically pump the water to the exterior.
Now You're Talkin' Like a Pro
We’ve created a guide for you to keep on hand so that you can understand relevant terms related to your product selection like a pro! Whether you are a contractor or a weekend warrior, understanding these terms will help to ensure that your goals are being met, the installation goes smoothly, and your project is a success.
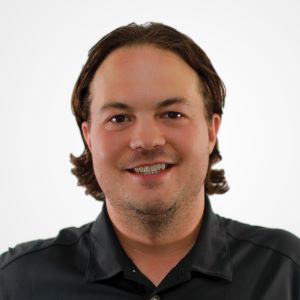
Written by Ryan Goodwin
Ryan Goodwin is the Pango® Product Manager at Stego Industries, LLC. He has been a part of the Stego team for over fifteen years with previous roles as the Regional Manager and Regional Director for Texas, Oklahoma, and Louisiana. As the Pango Product Manager, Ryan was a part of the team that developed Pango Wrap. Ryan appreciates working with design professionals, pest management professionals, and contractors to promote Integrated Pest Management practices and sustainable solutions for pest control.
- Stego (26)
- StegoCrawl (24)
- Stego-Awareness (17)
- Case Studies (14)
- StegoHome (14)
- StegoCrawl-Consideration (12)
- StegoCrawl-Awareness (11)
- Customer Stories (9)
- Stego-Consideration (9)
- Pango (8)
- Beast (7)
- StegoHome-Awareness (7)
- StegoHome-Consideration (7)
- How to Install (6)
- Drago (5)
- Pango-Awareness (5)
- Beast-Awareness (4)
- Beast-Consideration (3)
- Drago-Awareness (3)
- Pango-Consideration (3)
- Stego IQ (3)
- Drago-Consideration (2)
- StegoCrawl-Decision (2)
Popular Posts
Stay Connected.
Enter your email below.
Post Comments