A Deep Dive into Vapor Control Across the Building Envelope
PART TWO: 7 Takeaways to Help you Design, Evaluate, and Select the Right Water Vapor Control Layer for the First Side of Your New Home's Building Enclosure
This is part two of a two-part article. We recommend reading Clear Up Confusion Around Vapor Barriers with Basic Building Science before this one for context on baseline building science.
This article will focus on vapor control at the first side of the home (below the concrete slab or in a crawl space), but we’ll first look at above-grade walls for some helpful perspective. As we identified in the first article, concerns that surround vapor barriers in walls have occasionally been mistakenly applied to home foundations during new residential construction.
Vapor Barrier Use in Above-Grade Walls
The building code (2021 IRC Section R702.7) provides an oft-cited definition for “vapor retarders”. It outlines three Class levels of acceptable materials (Class I, II, or III) based on water vapor permeance. This Section of the code applies to vapor retarders on the interior side of framed walls and specifically excludes basement walls or the below-grade portion of any wall. Although it is not explicitly defined in the noted code Section, many in the building science world consider a Class I vapor retarder (less than 0.1 perms 1) as a relatively impermeable material. As such, materials with this level of permeance are often referred to as “vapor barriers”, at least from the perspective of the wall. The code offers prescriptive guidance on the wall vapor retarder based on Climate Zone, but considerations for project teams are often more nuanced.
Exterior walls, especially ones above-grade, interface with the outside, ambient environment. Outdoor conditions (air temperature, humidity, wind) differ depending on where we build, the time of year it is, etc. The contrast between the conditions of the ambient environment and the conditioned building envelope influences how a project team would look at designing a wall system that properly controls water, air, vapor, and heat.
Some areas of the country are hot and humid (i.e., there is more water vapor in the air) outside the home than inside as our HVAC system is working to maintain the level of comfort we want. So, in those areas (at least during a good chunk of the year) water vapor moves – again via diffusion - from outside the home into the building envelope.
In other areas of the country where it is colder and drier outside (again, at least for parts of the year) water vapor can tend to move in the opposite direction from inside the home to out. Water vapor can move in this “inside to out” direction because there can be a higher concentration of water vapor in the air within the building envelope (think about occupants breathing, showering, cooking, etc.) than outside.
1 1 US Perm = 1 grain/(ft2*hr*in-Hg)
How we control water vapor diffusion across a wall varies, not only in the use or disuse of a vapor control layer, but in its location in the wall assembly, both of which are affected by the expected direction(s) by which water vapor will tend to move and its potential impact on other components.
The historical thinking was in warm climates, a vapor barrier (that is Class I, like polyethylene sheeting) should be located on the exterior of the wall and in colder climates it should be on the interior of the wall assembly (behind the drywall). But what building science has come to find is that it’s not always that easy. After all, even generally categorized “cold climates” have home cooling seasons (where the AC is running) and “warm climates” still have colder ambient temperature in the winter. That means water vapor has the potential to move through the wall in either direction throughout most of the country, at some time of the year.
That becomes a potential problem if a “vapor barrier” is used in the wall and creates a surface on which water vapor can accumulate and condense, should that surface fall below the dew point temperature. In a wall system, this can be disastrous, as it could lead to mold growth or water damage to other wall assembly components, like insulation and wood framing. The same concerns exist when a vapor barrier is used on the interior of a framed and insulated below-grade basement wall.
That’s why building science has evolved to where, in most Climate Zones, the use of a low-permeance water vapor barrier in a wall assembly is generally not needed. Rather, the thought is wall systems are better off being designed to be relatively vapor “open” or, essentially, dry out if they get wet. In this practice, the vapor control layer (if one is used at all), may take the form of a “vapor retarder”, a material with a higher perm rating…intended to slow down water vapor diffusion, but not stop it.
Even more, it’s been well understood that the diffusion of water vapor through above-grade walls is actually fairly minimal in comparison to the amount of water vapor carried into the building via air movement. Usually due to gaps, holes, or other inconsistencies in the building envelope, advective transport of water vapor into the home -- as air rushes in -- is the more significant mechanism of potential moisture accumulation in walls. Thus, in wall systems, an effective air barrier (and air sealing) is generally much more important than controlling the movement of water vapor through diffusion.
There are even now “smart” wall membranes that act as both effective air barriers and provide variable vapor control depending on the relative humidity in the air around them.
The use and location of a vapor barrier (or vapor retarder) in a wall system is nuanced and not seen as a given. In many cases, a low-permeance (that is, impermeable or vapor closed) material, like polyethylene sheeting, may not have a useful place in above-grade wall systems, especially if located in the wrong spot.
But (BIG “but” here) - and this is important - the exterior wall is very different than the concrete floor slab or crawl space. Controlling vapor diffusion on the first side of the home’s building envelope must be evaluated and implemented separately.
The First Side of the Home is Different and Critical to Protect
Here is what is important to understand about water vapor protection during new residential construction on the first side of the home:
- the ground contains moisture, and
- water vapor diffusion is strong.
It doesn’t matter where you build, there is likely a replenishing source of water beneath your home. Even in the hottest, driest climates water vapor never stops emitting from the water table at some depth in the soil.
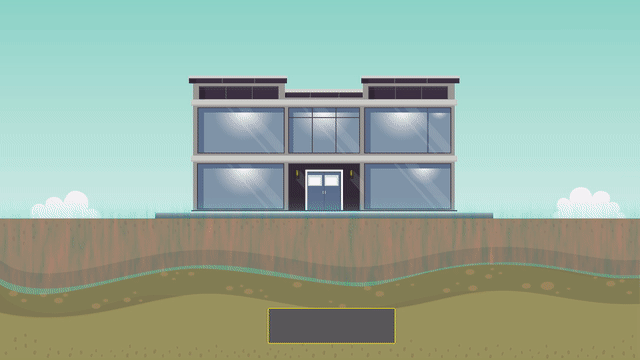
Construct a new home over the ground, especially when placing a concrete slab on or below-grade, and it won’t take too long until the relative humidity in the soil reaches at or near 100% beneath the home as water vapor rises through the soil column and accumulates below.
Another big difference is that in a wall system diffusion of water vapor is relatively minimal (like we describe above), but beneath the home the vapor drive is very strong.
Our soil is “wet”, yet our slab and interior are comparatively much drier, all year long, no matter where we build (unless your home is a steam room). So, beneath the home, diffusion is the primary mechanism for water vapor transport and is (generally) always moving in one direction, from outside the home (the soil) to in.
Moreover, because concrete is not vaporproof, if left unprotected the diffusion of water vapor will migrate through the slab over time and into the home’s interior – leading to potential flooring failures, mold growth, and just additional water vapor for the HVAC system to contend with.
This means isolating the home from the ground by controlling water vapor diffusion is absolutely critical – a vapor barrier is needed (and generally required…read on) regardless of geography, Climate Zones, how dry the soil appears, etc. And it should be located directly under the slab.
Side note: transport of water vapor through air can occur on the first side of the home (consider how radon gas very often migrates into a home). But it is diffusion’s contribution that is more significant, and the dominating “force” behind moisture migration within a slab. Also, keep in mind that because of its density, a concrete slab can be a decent air barrier. But concrete slabs crack and there are often joints, penetrations, etc. That means the vapor barrier beneath can also help serve a continuous air barrier function on this side of the home (and part of the radon or soil-gas mitigation system), but it needs to be installed well.
Definitions (of Performance) Matter
The under-floor space section of the code (2021 IRC Section R408) references the previously described Class I vapor retarder for ground cover in a crawl space. However, the section of the code for vapor retarders below concrete floors on ground (2021 IRC Section R506.2.3) does not.
This is a good thing. It would be a mistake to select a below-slab vapor retarder or barrier solely on one performance characteristic (in this case water vapor permeance), especially based on a definition outlined in the above-grade wall Section of the code. The code provides an absolute minimum level of performance. When it comes to water vapor protection for floor slabs and crawl spaces, there is additional guidance and best practices from the industry beyond the code.
ASTM E1745 is the governing standard specification (read: “performance standard”) for below-slab vapor retarders and barriers. Materials must test to and meet this standard and are expected to effectively impede water vapor diffusion over time to be considered for use below slabs. It’s also the performance standard referenced for crawl space soil-gas retarders in radon mitigation guides 2.
In addition to strength and conditioning (longevity) testing specifically suited for this below-slab application, ASTM E1745 provides a minimum requirement for water vapor permeance – less than 0.1 perms.
You may notice ASTM E1745 aligns with the Class I permeance threshold referenced in the building code. But, in the concrete and flooring world, this is the minimum for a below-slab water vapor retarder. A below-slab vapor barrier has an even lower industry-established definition as a material with a water vapor permeance of less than 0.01 perms (ACI 302.2R-06). A vapor barrier is recommended for concrete floor slabs which will – or could - receive moisture-sensitive floor covering (like hardwood, carpet, and laminates, among others), coating, or stored goods.
The use of flooring (or other coverings) over the concrete slab is a noteworthy distinction on its own. We are often creating a situation where we are knowingly (and somewhat unavoidably) putting a “vapor barrier” on top of the concrete slab: many flooring systems, adhesives, or goods greatly impede water vapor transmission.
But unlike an above-grade wall, the slab does not have the ability to dry out - water vapor certainly won’t move back into the soil if the relative humidity there is high, or a vapor barrier is in place. Without a vapor barrier below the slab to prevent the water vapor diffusion in the first place - that is, a vapor barrier beneath the slab with a lower permeance than the flooring on top - water vapor can accumulate, condense, and induce costly flooring failures over time. Water vapor needs to be controlled before it enters the slab to keep the concrete dry.
When it comes to the first side of the home, I wouldn’t get too caught up on terminology. What we call the material matters far less than how it performs: On the first side of the home, the lower the permeance to water vapor, the better.
2 AARST (American Association of Radon Scientists and Technologists) CCAH 2020 and RRNC 2020
We want to stop water vapor before it gets into the concrete slab, the crawl space, or the interior living space for the life of the home. The closer to zero perms the better. The industry-referenced less than 0.01 perms is a practical and achievable level we can expect with a high-performance and cost-effective engineered polyolefin vapor barrier film technology suited for this application.
Now that we’ve detailed the difference in performance and application of vapor barriers between walls and foundations, you can see how industry definitions (and understanding) of vapor retarder and barrier performance vary.
Not All Plastic (or Building Products) are Created Equal
The problems with generic poly sheeting (often 6-mil thick historically referenced in code language) beneath concrete slabs or in crawl spaces are well understood. Yet, it is still very common for new residential construction to use low-quality, recycled clear or black poly sheeting at the foundation. Not only have codes been evolving on the use of 6-mil poly under slab, but for decades guidance from the American Concrete Institute (ACI 332.1R-18), warranty requirements from flooring manufacturers, and even EPA guidelines have moved well past generic poly sheeting for this application.
It seems that the use of confusing nomenclature, long-standing habits of homebuilders or trades, and noted problems with poly sheeting in walls has perpetuated misunderstanding about addressing foundations.
Current industry best practice points to using a higher-performance membrane; again, with low-permeance, high-strength, and longevity beneath the slab or to cover the ground in a crawl space. In the plastic film landscape, this requires a greater level of raw material quality and engineering. Regardless of foundation type, vapor protection represents a component you get one good chance to do right.
Finally, we have noticed confusion around the use of other building materials at the foundation and their utility as a vapor retarder or barrier. For example, with insulation materials.
Sub-slab insulation may be a “vapor retarder” when using the definition outlined in the wall section of the code. But remember: beneath a slab, a vapor retarder must, at minimum, have a water vapor permeance of less than 0.1 perms (less than 0.01 perms is, in many cases, even better). Not only that, but to meet ASTM E1745 it must maintain the minimum permeance after mandatory conditioning testing (over the life of the home). Even closed-cell spray foam or XPS rigid foam insulation would have to be thick to get close to a baseline of 0.1 perms.
To be clear, I’m not discounting insulation at all. Insulation is an important control layer and critical to home energy performance and comfort. It is just important to be cognizant that other building materials (waterproofing is another good example) or specific products may not have the water vapor permeance or additional performance testing (such as compliance with ASTM E1745) to satisfy current industry requirements for below-slab vapor control.
The First Side of the Home Needs a Vapor Barrier
Although vapor barriers are a complex building envelope topic, when it comes to the first side of the home, it’s straight forward. Here are 7 simple takeaways:
- Water vapor tends to move via diffusion from the soil into the home regardless of location, geotechnical data, or Climate Zone.
- Whereas water vapor diffusion is relatively minimal in a wall assembly, it’s often the primary mechanism of water vapor movement at the foundation when liquid water is already effectively controlled.
- A vapor control layer (vapor retarder or barrier) used to isolate the home from the ground is ALWAYS beneficial and (likely) required.
- Whereas wall vapor retarders may have varying degrees of permeability based on Climate Zone and location in the wall, a below-slab (or crawl space) vapor retarder must have a permeance less than 0.1 perms.
- On the first side of the home, the lower the permeance the better - a vapor “barrier” beneath a slab is defined by many in the concrete and flooring industry as a material with less than 0.01 perms. A low-permeance vapor barrier is recommended when slabs will (or could) receive a sensitive flooring, coating, or stored goods.
- Vapor retarders and barriers used beneath slabs should meet ASTM E1745.
- Generic poly sheeting (and likely other building materials) may not meet current, above-code industry guidelines and best practice for use as effective water vapor control below a slab or in a crawl space.
With this understanding, hopefully you can now begin to design, evaluate, and select the right water vapor control layer for the first side of your next home build. We’re here to help.
If you want to learn more about above-grade wall control layers and other building science goodness, check out some of these resources:
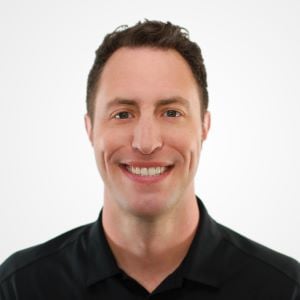
Written by Tom Marks
Tom Marks is the Business Development Project Manager with Stego Industries, LLC. He has been with Stego since 2007, serving many years as the Rocky Mountains Regional Manager. Now, his focus is geared toward vapor barrier solutions for new and existing homes as the Product Manager of the StegoHome and StegoCrawl brands. In addition, Tom serves as Sustainability Manager, overseeing Stego’s leadership in holistic product and corporate sustainability. Tom enjoys working with a wide range of project team members and customers to incorporate effective sub-slab vapor protection and create healthy, sustainable homes and buildings.
- Stego (26)
- StegoCrawl (24)
- Stego-Awareness (17)
- Case Studies (14)
- StegoHome (14)
- StegoCrawl-Consideration (12)
- StegoCrawl-Awareness (11)
- Customer Stories (9)
- Stego-Consideration (9)
- Pango (8)
- Beast (7)
- StegoHome-Awareness (7)
- StegoHome-Consideration (7)
- How to Install (6)
- Drago (5)
- Pango-Awareness (5)
- Beast-Awareness (4)
- Beast-Consideration (3)
- Drago-Awareness (3)
- Pango-Consideration (3)
- Stego IQ (3)
- Drago-Consideration (2)
- StegoCrawl-Decision (2)
Popular Posts
Stay Connected.
Enter your email below.
Post Comments